Well-managed preventive maintenance (PM) programs reduce equipment failures, increase machine reliability, and extend asset life. Maintenance managers who use preventive maintenance develop a more accurate, workable budget because they know which activities occur regularly.
In contrast, reactive maintenance, or a run to failure approach, lets machinery operate right up until it doesn’t causing budgets to balloon. Although there might be some situations where reactive maintenance makes sense, many more preventive maintenance examples exist to support the long-term benefits of PMs.
Five Preventive Maintenance Examples
Examples of preventive maintenance tasks include routine cleaning, lubricating moving parts, replacing worn-out components, and regular equipment repairs. These tasks are customized to the specific requirements of the equipment to ensure optimal performance and longevity. Scheduling these maintenance activities appropriately is essential and varies according to the type and usage of the equipment.
Preventive maintenance encompasses scheduled actions aimed at preventing equipment malfunctions and downtime. Typical examples involve regular system checks, timely software updates, thorough cleaning, and predictive replacements of critical components, all tailored to enhance performance and safety.
These five preventive maintenance examples represent critical yet standard activities routinely performed by reliability professionals.
1. Preventive Maintenance Equipment Inspections

Regularly scheduled machine inspections are a common example of preventive maintenance in action. Credit: Getty Images
Calendar-based inspections of facility equipment can represent one of the most critical preventive maintenance tasks routinely scheduled by maintenance managers. Regular inspections, including electrical boxes and HVAC units, ensure facilities properly operate and stay up and running. However, preventive maintenance can sometimes take a more critical turn depending on the facility.
For instance, preventive maintenance at a university or college is essential for ensuring students’ safe and comfortable learning environment inside and outside campus facilities. Maintenance professionals often use a Computerized Maintenance Management System (CMMS) software, such as eMaint, to automate inspection work orders and preventive maintenance tasks and document on-time completions. A CMMS helps support regulatory compliance when it’s time for an audit.
2. Clean Equipment Regularly to Minimize Dirt and Dust
Dirt and dust can destroy machinery, especially mechanical systems. It causes friction and premature wear. The contaminants that build up over time damage seals, cylinder walls, and other components inside of machines. Regularly cleaning those contaminants is another preventive maintenance example that shows how this simple strategy can extend machine life.
3. Lubricate Rotating Parts to Prevent Premature Wear
Lubricants keep critical machine parts moving. For example, a bearing failure could damage a machine and even harm associated machinery, causing a production shutdown. Regular lubrication is a great preventive maintenance example of how to keep machines up and running.
4. Check Machinery Power to Optimize Energy Efficiency
Controlling energy consumption is one of the most effective ways to significantly reduce costs. Create preventive maintenance tasks to regularly check and optimize assets, like HVAC systems, minimizing wasted energy.
5. Repair or Replace Equipment Before it Fails
PMs track and document machine health, letting maintenance professionals make better decisions. But preventive maintenance can also uncover machinery problems. For instance, after several routine preventive maintenance inspections, records show that the machinery also needs frequent corrective maintenance, it’s a strong sign that it’s time to replace the equipment to avoid further downtime or even failure.
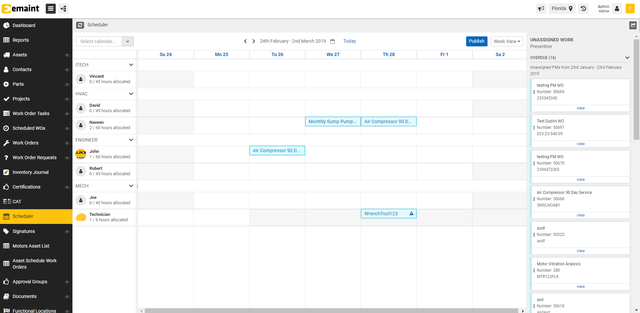
eMaint allows you to schedule regular inspections and build a preventive maintenance program.
Frequently Asked Questions about Preventive Maintenance
What is Preventive Maintenance?
Preventive maintenance encompasses a series of scheduled tasks designed to prevent equipment failures before they occur, enhancing safety and efficiency within operations. This approach involves regular, proactive maintenance to ensure that machinery and systems operate within their intended specifications, thereby minimizing downtime and extending the lifespan of equipment.
Preventive maintenance examples typically include tasks such as oil changes, filter replacements, parts lubrication, and comprehensive system checks. For instance, in a manufacturing setting, preventive maintenance might involve routine inspections of conveyor belts for wear and tear, adjustment of alignments, and calibration of control systems to ensure optimal performance. Similarly, in IT environments, preventive maintenance includes regular updates to software systems, checks on data backup processes, and hardware inspections to prevent data loss and system failures.
These routine services are crucial for maintaining the efficiency and reliability of equipment and play a significant role in safety and regulatory compliance. Regular preventive maintenance can help identify and rectify potential hazards before they pose a risk to operations or personnel.
By implementing a structured preventive maintenance program, companies can avoid the inconvenience and high costs associated with unplanned downtime and repairs. This proactive measure is considered an investment in the longevity and productivity of a company’s assets, ensuring that they perform reliably over time.
What is an Example of a Preventive Maintenance Service?
Preventive maintenance services are essential routines designed to keep equipment in optimal working condition and prevent unexpected failures. One typical example of preventive maintenance service is the periodic inspection and maintenance of industrial machinery. This service typically involves tasks such as lubricating moving parts to reduce friction and wear, replacing filters to ensure clean operation, and checking safety controls and software to ensure they function correctly.
These actions are crucial not only for the longevity of the machinery but also for the safety and efficiency of the entire operation. Regularly scheduled preventive maintenance can significantly decrease the likelihood of equipment breakdown, minimizing downtime and maximizing productivity. Furthermore, these services help businesses comply with regulatory standards and maintain a high level of quality control in their operations.
By integrating these preventive maintenance examples into their routine, companies can achieve better resource management, reduced operational costs, and improved equipment performance. This proactive approach is a cornerstone in the maintenance strategies of successful organizations, particularly those relying heavily on continuous and efficient machine operation.
How Preventive Maintenance Software Can Help?
Simultaneously juggling and organizing numerous preventive maintenance activities is no easy task. Maintenance and reliability leaders using eMaint CMMS software can efficiently and effectively manage PMs. Whether monthly or weekly routes or a daily cleaning inspection of food processing machines, leveraging CMMS software keeps everyone informed of upcoming PMs.
How Can You Add Predictive Maintenance Features to a Preventive Maintenance Program
Once professionals get comfortable with PMs, they often want to add predictive maintenance (PdM) strategies. A growing number of organizations use both preventative maintenance and predictive maintenance to keep machines running. Implementing maintenance software together with remote condition monitoring technology like wireless vibration sensors lets maintenance professionals take that next step from preventive maintenance to predictive maintenance.