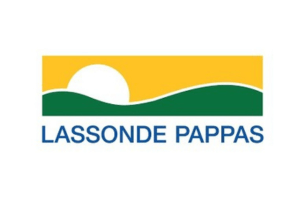
Lassonde Pappas Selects eMaint CMMS to Support its 24/7, Multi-location Operations
Customer Since: 2011 | Industry: Beverage Processing
Lassonde Pappas produces millions of cases annually of organic and conventional juices, ready-to-drink teas, enhanced waters, and cranberry sauces. CPC wanted a CMMS solution that could reduce maintenance spending and inventory cost while increasing asset health at their US locations. Within a month, assets, work order templates, and reports were accessible through the system, and over 150 PM tasks were defined and applied to related assets. eMaint has been successful in helping CPC, and the company continues to find new, interesting ways to make the software work for their needs.
BACKGROUND
Lassonde Pappas is a subsidiary of Lassonde Industries, Canada’s largest food manufacturer. CPC produces millions of cases annually of organic and conventional juices, ready-to-drink teas, enhanced waters, and cranberry sauces. James Hummer, Maintenance Manager of the Hendersonville, NC plant, joined a team of 15 maintenance technicians at Lassonde Pappas in May, 2011. James served in the US Navy as a maintenance mechanic for 16 years, earned a degree in Workforce Education and Development and has previously worked for several food and beverage processors. James first worked with the eMaint system at Gatorade in 2006. When Lassonde Pappas realized their current CMMS did not meet their needs, eMaint CMMS was chosen.
THE CHALLENGE
CPC sought a system that could reduce maintenance spending and inventory cost while increasing asset health at their US locations. A goal was set to increase their current uptime rate by 30% within two years. PM procedures were put in place for their production assets which include conveyors, chillers, fillers, bottlers and sterilization equipment with a goal to achieve 95% PM compliance and completion. Regulations within the food and beverage industry require that CPC comply with annual Safe Quality Food audits, OSHA, and FDA standards. Reports were needed to demonstrate compliance.
IMPLEMENTATION
The initial pilot program began at CPC’s California and Hendersonville plants with a goal of rolling it out across all US locations. Within a month, assets, work order templates, work request templates, and reports were accessible through the system. Over 150 PM tasks were defined and applied to related assets. Lassonde Pappas utilized the system to develop accurate bills of materials, set inventory reorder levels and define inventory reports that would hold contractors accountable for inventory and help drive down inventory carrying costs. Sharing inventory between plants (critical spares, in particular) will allow inventory levels to be lower without impacting uptime. Several different work order types were established for planned and unplanned work including corrective work identified during preventive maintenance checks (CmPm).
Emergency requests are auto-approved and set to a high priority. They have established a process of post-analyzing each repair and then optimizing their PM procedures moving toward a world-class goal of 80% planned maintenance and 96% uptime. The scheduling feature allows CPC to maximize productivity and measure actual performance against standards.
BENEFITS
“The ability to define a PM procedure once and apply it across multiple related assets (such as tabletop conveyors) significantly shortened implementation time allowing us to be operational within a month.”
James H., Maintenance Manager, Lassonde Pappas