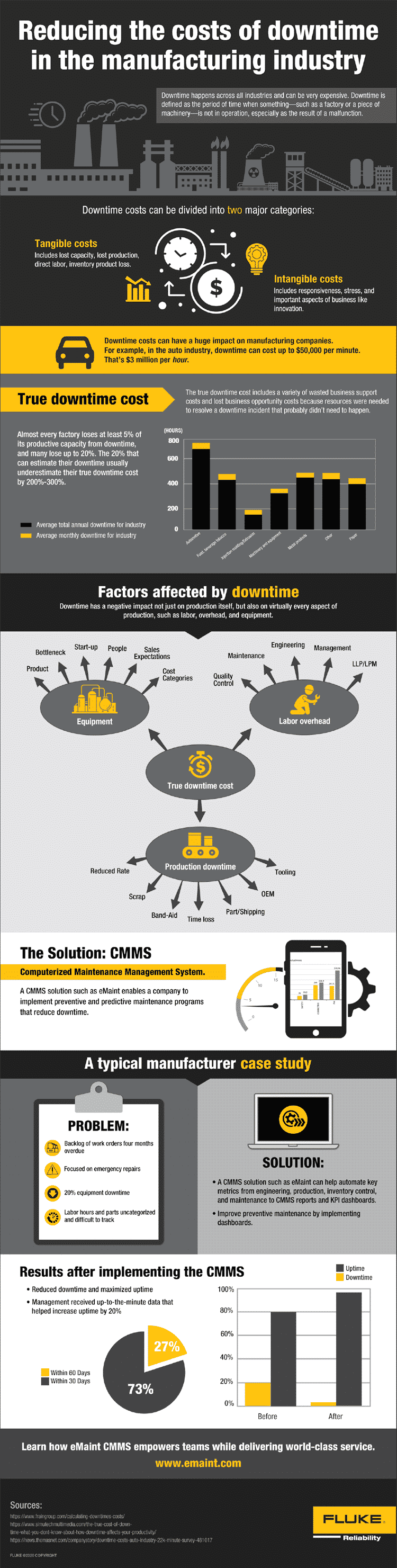
Costs of Downtime in the Manufacturing Industry
Across all industries, downtime happens and it can be very expensive. Downtime is defined as the period of time when something, such as a factory or a piece of machinery, is not in operation, especially as the result of a malfunction.
Downtime can divided into two major classes:
- Tangible costs, which are relatively easy to quantify. They include lost capacity, lost production, direct labor and inventory product
- Intangible costs, which are difficult to put a dollar figure on, but may be even more significant than tangible costs, These include responsiveness, stress and important aspects of business like innovation.
True Downtime Cost
The true downtime cost includes a variety of wasted business support costs and lost business opportunity costs. In fact, almost every factory loses at least 5% of its productive capacity from downtime, and many lose up to 20%. Some of the factors affected by downtime include:
- Equipment availability for production, sales expectations, bottlenecks and more
- Labor overhead for quality control, maintenance, engineering and management
- Production downtime, resulting in time loss, reduced rates, scrap, band aids and more
The Solution
The solution to reduce downtime is through preventive and predictive maintenance programs. A CMMS solution such as eMaint can help automate key metrics from engineering, production, inventory control and maintenance to CMMS reports and KPI dashboards. In a typical manufacturer case study, dashboards gave management up-to-the-minute insight into:
- Downtime by production line
- Work order aging
- Work order throughput
- Open work orders by type
This data helped increase uptime by 20%, and completion of backlogged work orders increased significantly.
Embed Infographic on Your Website or Blog: