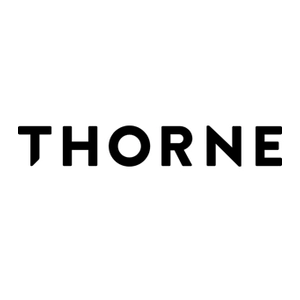
Thorne HealthTech Boosts FDA Compliance and Optimizes Inventory Management with eMaint
Customer Since: 2022 | Industry: Health Technology
Summary
See how Thorne HealthTech used eMaint for regulatory compliance, inventory optimization, and improved decision-making processes across its plant.
- Optimized parts storeroom and inventory management
- Developed a deep understanding of labor and parts costs for each asset
- Shifted from a reactive maintenance system to a proactive maintenance approach
- Improved decision-making processes around machine maintenance and replacement
- Enhanced capital planning for future asset replacements
BACKGROUND
Thorne HealthTech is a leader in developing the world’s most innovative solutions for a personalized approach to health and well-being. It is a science-driven wellness company that empowers individuals with the support, education, and products they need to lead healthy, active lives.
Thorne takes great pride in the science behind its formulations, ingredients, manufacturing process, and finished products. Their supplements are trusted by thousands of professional athletes, including 11 U.S. national sports teams.
The company began using eMaint in 2022 and has since seen more ease during compliance audits, improved spare parts organization, and a company-wide shift to proactive maintenance.
CHALLENGES
Thorne HealthTech specializes in personalized wellness solutions such as supplements and health tests. Part of its commitment to its customers includes clean manufacturing processes and maintaining rigorous certifications such as the U.S. Food and Drug Administration’s (FDA) Current Good Manufacturing Practice and being NSF Certified for Sport.
“A huge part of our decision to go with eMaint was because our account has to be validated by the FDA,” said a maintenance supervisor for Thorne HealthTech. “They go through and test everything and need to know everything is working as it should.”
Prior to using eMaint, Thorne kept work orders on paper and its inventory on an Excel spreadsheet which technicians had to edit manually. With over 10,000 work orders annually, it was impossible to trace machine history.
During FDA audits, Thorne staff would often have to search through boxes of paper to find the records they requested. Additionally, the inventory spreadsheet was often not updated correctly, and maintenance technicians never knew if something was in the parts storeroom without physically checking.
IMPLEMENTATION
The shift to eMaint’s system began with the Thorne HealthTech team working closely with eMaint’s implementation experts to customize the software. Their goal was to gain clarity about the organization’s workflow.
Not only did Thorne need to know what type of maintenance was performed on each asset, they wanted to have an accurate work history for each asset. That included maintenance labor costs so that managers could make more effective decisions about proactive maintenance and purchasing replacement equipment.
Next, Thorne conducted a parts inventory to make sure it correctly added inventory to the new system and had an accurate count of every part on hand. Finally, eMaint conducted in-house training so that all staff members were ready to begin using the software when it rolled out.
“The support that we got during implementation was impeccable,” said the maintenance supervisor. “The staff at eMaint always knew where we were in the process and guided us in the right direction. They were always willing to help.”
RESULTS
Thorne staff have seen immediate benefits from using eMaint. Inventory management runs a lot smoother, machine replacement decisions can be made effectively and efficiently, and FDA audits go by without a hitch.
The optimized storeroom has given Thorne new insight into inventory levels which have led to quicker maintenance turnaround times and cost savings. “We have a really good idea of what’s actually in our inventory,” the maintenance supervisor we spoke to said. “I have a database of parts that we already have, and I can have parts on hand before we start a project.”
Since Thorne began using eMaint in July 2022, it has completed nearly 25,000 work orders. “If we were doing that on paper, there’s no way that I could ever get a machine history or know what parts we used to get an accurate min/max value for keeping inventory,” he added.
Now that the team has a comprehensive machine history readily available, detailing the parts used for each machine, the maintenance supervisor is better equipped to provide reports on labor and parts costs to the Vice President of Engineering. He emphasizes that this information has significantly facilitated decision-making regarding machine replacement.
One of the best results has been the way eMaint supports Thorne’s commitment to its customers to keep manufacturing clean and traceable. Instead of tracking work orders on paper, the company knows exactly what happened to each asset, when it happened, and who completed the repairs.
The result has been a complete transformation in the way Thorne handles audits. “We can trace everything that we do,” said the maintenance supervisor. “We have electronic signatures and the exact times when something happened. When we get audited, we never have any problems.”
“eMaint has really helped us move from a reactive type of system to a more plan-type of work. It’s changed the way I work by giving me more time and having more data in my hands.”
– Maintenance Supervisor at Thorne HealthTech