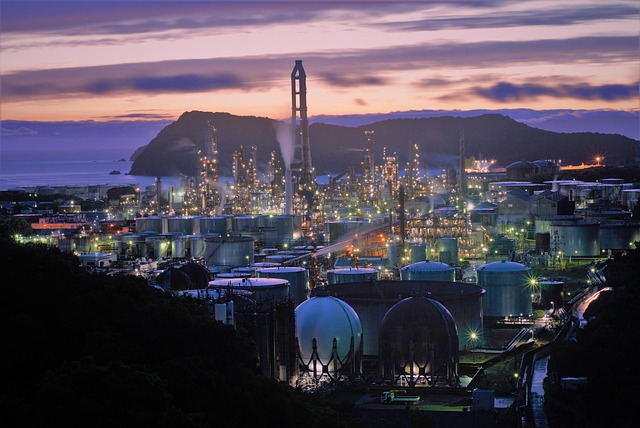
What is Industrial Maintenance?
Industrial maintenance is the practice of maintaining industrial machines and preventing breakdowns. Industrial maintenance involves regular upkeep, emergency repairs, and long-term preventive/predictive strategies. It’s also called plant maintenance, as it often refers to industrial plant assets. The goal of industrial maintenance is to reduce downtime, increase asset longevity, and strengthen overall asset reliability. Poorly running machinery consumes excessive energy, leads to wasted materials, and causes costly downtime. This crucial practice ensures that manufacturing plants, factories, and other industrial facilities operate efficiently, safely, and with minimal downtime.
When industrial maintenance teams can keep assets running as designed, it helps maximize safety, output, and uptime, boosting the bottom line. Activities like the servicing, repairing, and replacement of machine assets — from as small as a bearing to as large as a building — in an industrial setting fall under the umbrella of industrial maintenance.
Industrial maintenance involves a range of activities, including regular inspections, preventive maintenance, corrective repairs, and the use of advanced monitoring technologies to predict and prevent failures.
Industrial maintenance is vital for several reasons:
- Operational Efficiency: Regular maintenance helps ensure that equipment operates at peak performance, reducing the likelihood of unexpected breakdowns that can disrupt production schedules.
- Safety: Properly maintained equipment is less likely to fail in ways that could harm workers, making industrial maintenance a key component of workplace safety.
- Cost Savings: By preventing major breakdowns and extending the lifespan of equipment, industrial maintenance can save companies significant amounts of money in the long run.
- Regulatory Compliance: Many industries are subject to strict regulations regarding equipment maintenance. Adhering to these standards is essential to avoid fines and legal issues.
Common Industrial Maintenance Jobs & Types of Workers
Industrial maintenance requires a diverse workforce with various skills and expertise. Here are some common jobs and types of workers involved in industrial maintenance:
- Maintenance Technicians:
- Role: Perform routine inspections, repairs, and servicing of industrial equipment. They diagnose issues, replace faulty components, and ensure machinery operates smoothly.
- Skills: Technical knowledge of machinery, problem-solving abilities, and proficiency in using various tools and equipment.
- Maintenance Engineers:
- Role: Develop and oversee maintenance strategies to ensure equipment reliability. They analyze performance data, recommend improvements, and implement preventive maintenance plans.
- Skills: Engineering expertise, analytical skills, and experience with maintenance planning software.
- Reliability Engineers:
- Role: Focus on improving the long-term reliability of equipment. They study failure data, identify root causes, and develop strategies to enhance equipment reliability and minimize downtime.
- Skills: Strong analytical abilities, knowledge of reliability engineering principles, and experience with predictive maintenance technologies.
- Maintenance Managers:
- Role: Oversee the entire maintenance department, ensuring that all activities are carried out efficiently and effectively. They manage resources, coordinate schedules, and ensure compliance with safety and regulatory standards.
- Skills: Leadership and management skills, strategic planning, and knowledge of maintenance best practices.
- Condition Monitoring Technicians:
- Role: Use advanced monitoring tools and technologies to assess the condition of equipment in real time. They collect and analyze data to predict potential failures and recommend timely interventions.
- Skills: Proficiency with monitoring technologies, data analysis skills, and attention to detail.
- Planners and Schedulers:
- Role: Responsible for planning and scheduling maintenance activities. They ensure that maintenance tasks are carried out at the right time, with minimal disruption to operations.
- Skills: Organizational and planning skills, experience with scheduling software, and the ability to balance maintenance needs with production demands.
Each role within an industrial maintenance team is crucial for ensuring the efficient and reliable operation of machinery and equipment. By working together, these professionals help prevent unexpected failures, optimize maintenance schedules, and improve overall equipment performance.
Which Industries Use Industrial Maintenance?
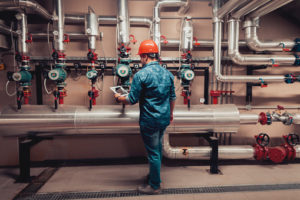
Industrial Maintenance Worker
Industrial maintenance is a vital component across numerous industries, each with specific needs and challenges. Here are some of the major industries that rely heavily on industrial maintenance:
- Manufacturing:
- Overview: Involves the production of goods using machinery and labor. Maintenance is crucial to ensure continuous production and prevent costly downtimes.
- Key Maintenance Activities: Regular inspections, preventive maintenance, condition monitoring, and predictive maintenance to keep production lines running smoothly.
- Energy and Utilities:
- Overview: Includes power generation, water treatment, and utility services. Maintenance ensures reliable service delivery and compliance with safety regulations.
- Key Maintenance Activities: Scheduled inspections, real-time monitoring, and advanced diagnostics to maintain infrastructure and prevent service interruptions.
- Oil and Gas:
- Overview: Involves exploration, extraction, refining, and distribution of oil and gas. Maintenance is essential to ensure safe and efficient operations.
- Key Maintenance Activities: Corrosion control, regular inspections, condition-based maintenance, and the use of predictive analytics to prevent failures.
- Transportation and Logistics:
- Overview: Covers the movement of goods and people. Maintenance ensures the reliability and safety of vehicles, aircraft, ships, and infrastructure.
- Key Maintenance Activities: Routine servicing, component replacements, safety inspections, and adherence to regulatory standards.
- Food and Beverage:
- Overview: Involves the processing and packaging of food and beverages. Maintenance is critical to ensure product quality, safety, and compliance with hygiene standards.
- Key Maintenance Activities: Cleaning, calibration, lubrication, and regular inspections to maintain equipment and prevent contamination.
- Pharmaceuticals:
- Overview: Involves the production of medicines and medical devices. Maintenance ensures the precision and reliability of production equipment.
- Key Maintenance Activities: Preventive maintenance, regular inspections, calibration, and strict adherence to regulatory requirements to ensure product quality and safety.
- Mining:
- Overview: Involves the extraction of minerals and raw materials. Maintenance is essential to ensure the reliability and efficiency of heavy machinery and equipment.
- Key Maintenance Activities: Regular servicing, component replacements, system checks, and the use of advanced diagnostics to prevent breakdowns.
Examples of Industrial Maintenance
Conveyor Belt Maintenance: Conveyor belts are critical components in many industrial processes, particularly in manufacturing and material handling. Routine maintenance for conveyor belts involves several key tasks:
- Inspection: Regularly checking for wear and tear, misalignment, and damage to the belt and its components.
- Lubrication: Ensuring that bearings, rollers, and other moving parts are properly lubricated to reduce friction and wear.
- Belt Tensioning: Adjusting the tension to prevent slippage and ensure smooth operation. Too much or too little tension can cause operational issues and accelerate wear.
HVAC System Maintenance: Heating, ventilation, and air conditioning (HVAC) systems are vital for maintaining a controlled environment in industrial facilities. Common maintenance tasks for HVAC systems include:
- Filter Replacement: Regularly replacing air filters to maintain air quality and system efficiency.
- Coil Cleaning: Cleaning the evaporator and condenser coils to improve heat exchange efficiency and prevent system overload.
- Inspection and Calibration: Checking thermostats and control systems to ensure they are functioning correctly and calibrating them as needed to maintain desired temperature and humidity levels.
Pump and Motor Maintenance: Pumps and motors are essential for various industrial applications, from water supply to process control. Maintenance tasks for these components often include:
- Alignment Checks: Ensuring that motors and pumps are properly aligned to avoid excessive vibration and wear.
- Lubrication: Regularly lubricating bearings and other moving parts to minimize friction and prevent overheating.
- Performance Testing: Monitoring and testing the performance of pumps and motors to detect issues such as reduced flow rates or abnormal noises, indicating potential problems.
Industrial Maintenance Strategy
Industrial machinery, from common assets like motors to sophisticated systems like wind turbines, follows a lifecycle from installation to operation and eventually, end-of-life or breakdown. Maintenance is key to optimizing equipment lifespan—making sure assets perform effectively for as long as possible.
We often think of maintenance as an emergency response to faults, failures, or total breakdowns, and it’s true that industrial maintenance work is often reactive firefighting. Maintenance is vital to employee safety, like when ammonia compressor fails and toxic gas leaks. It’s also essential for compliance with key regulations from OSHA to FDA and IATF. And of course, maintenance keeps production going and revenue flowing: a worn bearing on a key engine may shut down an entire production line.
But relying on reactive or breakdown maintenance can be disastrous—wasting time, labor, money, and slowing down production.
Forward-looking maintenance strategies are the answer. Maintenance and reliability teams can harness the power of preventive, condition-based, and predictive maintenance to maximize uptime.
- Reactive maintenance is performed in response to machine assets having issues, ranging from minor faults to major failures. Reactive maintenance, also known as “run-to-failure” maintenance, is only performed when problems arise. A reactive approach is ideal for easily-replaceable parts like lightbulbs, but can be problematic for complex and/or critical industrial machines.
- Breakdown maintenance is a strategy in which workers wait until a machine fully breaks down or is out of operation before performing maintenance work. A breakdown maintenance strategy can make sense for non-critical assets, but can be dangerous and costly when applied to production-critical machines.
- Preventive maintenance (PM) strategy involves planning regular maintenance to prevent faults and failures. Preventive maintenance is scheduled based on regular time intervals or equipment usage intervals. A PM approach to industrial maintenance reduces the risk of asset downtime and is important for essential assets.
- Condition-based maintenance (CBM) is work done in response to asset condition data, like vibration or temperature levels, that gives insight into machine health and informs whether maintenance is needed. CBM is vital for sophisticated machines that need to be monitored.
- Predictive maintenance (PdM) is maintenance work performed in advance that is informed by predictive data, like detailed vibration data captured by wireless sensors. Predictive maintenance is a powerful tool for maxing the uptime and strengthening the reliability of your most critical assets.
- Reliability-centered maintenance (RCM) is a framework that focuses on the big picture: what maintenance strategy is best for each asset or type of asset to achieve cost-effective uptime? A reliability-centered strategy calls on whatever approach is best for the job, from breakdown to PdM. Reliability-centered maintenance often involves Asset Criticality Analysis (ACA), Failure Modes and Effects Analysis (FMEA), and Fault Tree Analysis (FTA) as methods to analyze assets and determine the ideal gameplan.
How do industrial maintenance teams manage and implement these strategies across their maintenance programs?
That’s where maintenance software comes in.
Why Use Industrial Maintenance Software?
Industrial maintenance teams need maintenance software to manage, plan, and execute a winning maintenance strategy.
Maintenance software serves as a command center for work orders, asset management, spare parts inventory, maintenance KPI reporting, and much more. Leading maintenance management software also offer mobile apps, condition monitoring, integrations with key business systems, and global, multi-site capabilities.
Common software types include Computerized Maintenance Management (CMMS) systems and Enterprise Asset Management (EAM) systems, which often overlap.
A CMMS or EAM empowers industrial maintenance teams to save time, simplify their work, cut costs, prevent downtime, and increase overall asset reliability.
eMaint CMMS can track all of the work done on every asset. When teams track, trend, and analyze asset condition data, they can make better decisions, prioritize their scheduling and spending, and reduce costs.
Increased visibility into industrial maintenance activities enables teams to identify trends, adapt to changing priorities, and improve their communication and processes. Centralizing all documentation — from contracts to manuals — simplifies the compliance process and ensures that maintenance team members can securely access the information they need anytime and anywhere.
To make the most of your industrial maintenance program, you need to define your goals and targets. A computerized maintenance management system (CMMS) software can track metrics, generate reports, and deliver insights you can use to reach your goals.
Learn more about eMaint CMMS.