What is Asset Performance Management (APM)?
Asset performance management (APM) is a strategic methodology employed by businesses to enhance the efficiency and reliability of critical assets used in daily operations. Companies leverage APM to optimize the functionality of diverse assets such as infrastructure, machinery, vehicles, and digital systems to maximize productivity and minimize downtime.
APM is all about pairing modern maintenance software with technology like sensors to amplify asset management. Collecting condition monitoring data and analyzing it with software analytics can help reduce asset failures and unplanned downtime, ultimately extending an asset’s useful life.
Most maintenance teams already use a computerized maintenance management system (CMMS). CMMS software puts all of an organization’s maintenance information, processes, and tasks in one place. From work orders to inventory management and much more, CMMS software is a vital component of optimizing a maintenance strategy.
Asset performance management software takes your CMMS to the next level by feeding it real-time machine health data. Examples of assets included in APM programs are motors, fans, pumps, machines, vehicles, and more.
When you know how and when your assets are likely to fail, you can plan and take action, reduce risks, and increase your reliability.
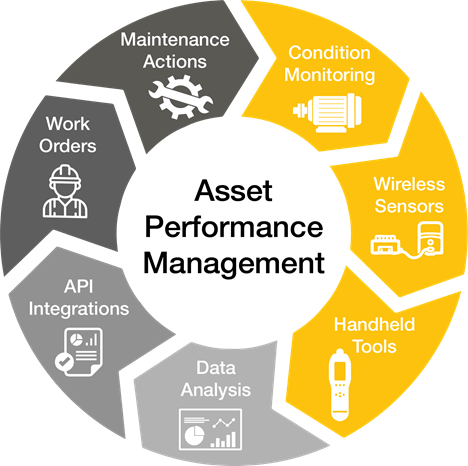
What are the benefits of using APM software?
With asset performance management software, you can turn data into insights. Data alone is not truly valuable until it is given context — and made actionable. APM software collects and analyzes information from your machines and makes it easier to make better decisions about when to take action to meet maintenance and performance goals.
Making the most of asset performance means reducing the costs and risks at all stages of an asset’s lifecycle, from design to decommissioning. APM helps teams use real-time knowledge to tackle today’s challenges and look ahead to prepare for tomorrow’s.
How to Measure Asset Performance
Asset performance can be measured in several ways. Depending on your organization and the assets themselves, certain key performance indicators (KPIs) can give you insights into how assets are performing. This information plays an important role in your asset performance management strategy.
The more data you have about each asset, the easier your job will be as you set out to develop your APM. You can measure an asset’s performance against its historical performance over time, and also compare it to other similar assets to gain insight.
Here are a few of the most important KPIs to consider:
Mean Time Between Failures
Mean time between failures (MTBF) is a KPI indicating the length of time between repairs for each asset. This number is normally expressed in hours. It also doesn’t include planned maintenance. Instead, it tells you how long each asset stays up and running before needing to be repaired.
The goal of an asset performance management program is to increase the number of hours between repairs, resulting in a longer asset lifecycle and a decrease in unplanned downtime.
Overall Equipment Effectiveness
Overall equipment effectiveness (OEE) is another asset performance KPI. This KPI measures the availability, performance, and production quality of the equipment over the time measured.
After you implement your asset performance management program, you should start to see improvements in OEE scores for your assets.
Mean Time to Repair
Mean time to repair (MTR) measures the average time it takes to repair an asset and return it to operation.
MTTR can be improved through better maintenance practices, such as predictive maintenance to catch and correct problems before they become major issues with longer repair times.
How to Build an APM Program
Building a successful APM program starts with gathering and analyzing information about the assets you have, along with their maintenance history. If you’re already using a CMMS, this could be as simple as running a report. However, if you’re using spreadsheets or have paper maintenance records, gathering and analyzing data could be an enormous undertaking.
You’ll also need to know which assets are most critical to your organization. These are the assets that, when they break down, can completely shut down production or significantly impact other assets. An asset criticality analysis identifies these assets, and as you build your APM program, you can prioritize the assets that are most important to your operation.
Next, build a plan to optimize each asset’s maintenance schedule. A truly optimized maintenance schedule takes planned maintenance into account, scheduling it during planned downtime to maximize both uptime and employees’ schedules. But an effective asset performance management program also implements predictive maintenance (PdM), adding insights from sensors or other data to maximize maintenance practices.
Predictive maintenance gives insights into asset health and helps teams find and fix developing issues before they cause machine failure. Asset performance management software can assist with scheduling and managing both planned and predictive maintenance schedules.
The final step is to monitor asset data to determine the success of your APM program. Like any process on the production floor, your APM program should be continuously improved so you receive the maximum benefit from the program. As you continue gathering data, you can make small changes to create an even more effective asset performance management program.
Asset Performance Management and Predictive Maintenance
Today, maintenance teams are increasingly turning to predictive maintenance. By using condition monitoring sensors and software to track asset health, they can catch potential failures before they cause damage or unplanned downtime.
A study by the Deloitte Analytics Institute found that, on average, predictive maintenance both increases productivity and lowers maintenance costs by 25%. It also reduces equipment breakdowns by 70%.
Productivity, uptime, unplanned downtime, and maintenance costs are a few metrics organizations can track to learn how effective their maintenance strategy is. When a team tracks its metrics and monitors its effectiveness, it can find opportunities for continuous improvement.
Today, maintenance teams are increasingly turning to predictive maintenance. By using condition monitoring sensors and software to monitor asset health, they can catch potential failures before they cause damage or unplanned downtime.
A recent study by the Deloitte Analytics Institute showed that, “On average, predictive maintenance increases productivity by 25%, reduces breakdowns by 70% and lowers maintenance costs by 25%.”
Productivity, uptime, unplanned downtime, and maintenance costs are a few metrics organizations can track to learn how effective their maintenance strategy is. When a team is tracking their metrics and monitoring their effectiveness, they can find opportunities for continuous improvement.
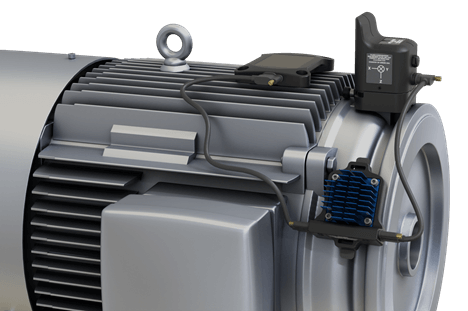
Integrating Condition Monitoring sensors and software
However, many organizations have cobbled together an ad hoc suite of tools over the years to manage and monitor their assets. This increases the likelihood of blind spots, where organizations are missing out on key insights about their assets. Operational silos keep teams from being able to truly leverage asset performance management.
As a result, it’s critical to integrate all of your tools into a centralized system to gain accurate insights and have a clear sense of priorities to act on. APM makes that possible.
How to leverage Asset Performance Management
An increasing number of technologies are shaping asset performance management today. Here are some making it possible for teams to make the most of asset performance:
- Data availability: Making better decisions about assets is only possible with accurate, high-quality data. Today, this data is more available than ever. Asset performance management software makes it possible to collect data about each asset’s current performance as well as maintenance history. Users can run reports and use that information to assist with decision-making processes about asset repair and replacement.
- Cloud storage: A cloud-based CMMS offers agile, scalable asset performance management that can still be accessed even if local computers go down. Users can monitor assets remotely and schedule needed maintenance, even if they can’t be on-site.
- Condition monitoring sensors: Condition monitoring used to require a knowledgeable human to be available on-site in order to manually check on assets. But now, condition monitoring sensors can monitor and collect temperature and vibration information, sending the information to the cloud for processing and analysis. On- or off-site users can monitor for problematic changes and request maintenance to correct potential failures before they happen.
- Artificial intelligence: When combined with a CMMS and condition monitoring sensors, automatic AI analysis can identify potential faults and prescribe maintenance recommendations, enhancing asset performance management without requiring extra staff to monitor assets.
All of these features simplify asset performance monitoring and provide insight and tools to help develop and improve your asset performance management strategy.
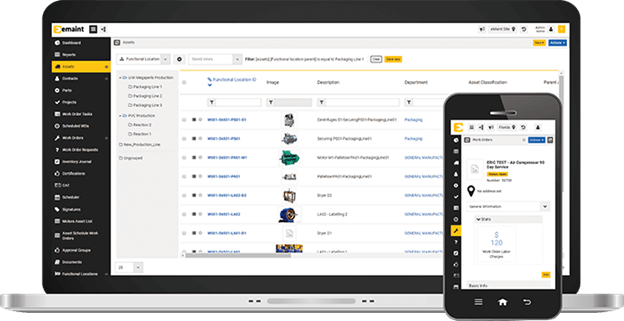
What is the difference between APM and EAM?
Enterprise asset management (EAM) is a strategy, not a software. Following an EAM strategy helps organizations monitor and track their assets and overall asset health in order to maximize asset performance and lifespan.
Work order management is one of the key elements of EAM. Digital management of work orders increases on-time work completion, improves response times, and streamlines the process of maximizing peak performance.
EAM, as indicated by “enterprise,” has a wide scope that goes beyond asset lifecycle management to include areas such as safety initiatives and financial management. And “assets” can refer to anything from machine components to buildings and plants. Assets are simply physical assets an organization needs to carry out its mission. EAM is a broad strategy that touches many areas of an organization.
APM, on the other hand, is different in two main ways. It has an explicit focus on helping organizations reach operational excellence by getting the most out of every asset. The insights and decisions that APM focuses on are those that maximize asset availability and uptime.
The other way APM differs from EAM is that it is more focused on real-time insights and data about assets, and less on record-keeping and communication. As technologies such as AI and condition monitoring sensors become more and more accessible, APM will be an attainable strategy for more organizations.
How to implement APM software
Demand for APM software is increasing as more organizations realize the value of combining software and sensors to maximize asset performance. APM software helps asset-intensive organizations get a connected, centralized view of all of their assets and needs.
To make the most out of an APM software implementation, your organization will need to pilot and adopt Industrial Internet of Things (IIoT) technologies like vibration sensors that can monitor assets. You’ll also need to find a maintenance software program that can integrate that machine health data with your organization’s other maintenance management processes.
The implementation process looks different for every organization, though the markers of success are often the same. Clearly-defined needs and goals are crucial to a successful implementation. Identify specific places where you seek to improve — such as reducing spending in a particular area of your maintenance budget — in order to help focus your work and planning during the implementation process.
The two main factors that contribute to failed implementations are poor project planning and lack of long-term vision.
If you don’t already have a CMMS, using one can mean the difference between failure and successful APM implementation. To see how eMaint’s CMMS works, check out a demo here.