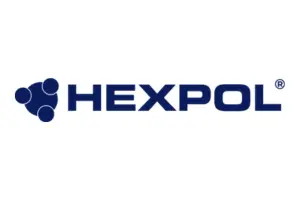
HEXPOL Compounding Americas Standardizes Maintenance Across 16 Sites with eMaint and Reduces Downtime
Customer Since: 2018 | Industry: Chemical Processing
HEXPOL Compounding Americas is a custom rubber manufacturer with 16 facilities spread across the U.S. and Mexico. Before implementing eMaint, each of the 16 plants was operating as a silo. This fragmented approach made it challenging for leadership to gauge maintenance efficiency and identify ways to improve operational KPIs across the board. They needed a way to unify their processes and create a consistent system for managing operations — so they turned to eMaint.
The company now uses eMaint to standardize processes and track key metrics across all its locations. This has allowed HEXPOL to optimize the productivity and maintenance of its assets in each facility, all while reducing costs and downtime.
With eMaint, HEXPOL has:
- Standardized maintenance and operations of 50 manufacturing lines across 16 sites
- Applied learnings across sites – such as creating a failure mode library – to increase efficiency and reduce downtime
- Streamlined and improved their inventory management processes
BACKGROUND
HEXPOL Compounding Americas (HCA) is a custom rubber manufacturer with 16 locations throughout the U.S. and Mexico. HCA’s parent company, HEXPOL AB, is based in Malmö, Sweden.
HCA manufactures rubber compounds for parts used in the automotive industry, such as seals, tires, and hoses, as well as materials for other sectors, including aerospace, consumer electronics, and energy.
Thanks to innovative processes and cutting-edge equipment, HCA produces products for customers that meet exacting specifications and can withstand the toughest conditions. They operate over 50 manufacturing lines in North America.
CHALLENGES
HCA grew quickly, in part through acquisitions, and by 2017 was operating largely as a decentralized organization. Many of its sites were functioning as independent and siloed units. This resulted in varied operational practices across the company, complicating efforts to deliver consistent results.
“It was challenging to understand what each site was doing and how they were doing it,” says John Sedgwick, Director of Engineering and Maintenance. “When problems would come up, it was very difficult to figure out how to work around them, because learning one system thoroughly is already hard. Learning eight to 10 different systems is even more challenging.”
To address this, the HCA team turned to eMaint Computerized Maintenance Management System (CMMS) to untangle the complexities in their operations and focus on consistency and cohesion.
IMPLEMENTATION
Implementing eMaint CMMS involved considerable planning and preparation, which has ultimately helped HCA gain more visibility and clarity across the entire organization. “Our first step was to standardize with a CMMS, then move toward standardizing our workflows, from work order entry to execution, auditing, and, ultimately, measuring our performance,” said Sedgwick.
The HCA implementation team quickly realized that a CMMS like eMaint doesn’t just highlight assets that need attention, it also helps measure the KPIs that will add the most value and uncover processes that can be improved.
For example, using the parent-child asset hierarchy within eMaint allows HCA to drill down and pinpoint which assets are at the root of a problem. HCA engineers could then build additional preventive actions around those assets, helping them stay ahead of any potential issues.
RESULTS
With eMaint, HCA was able to create a standardized maintenance system across all of its 16 sites, which Sedgwick credits to the CMMS’s customizability.
“Most systems are very rigid and standard, but eMaint allows you to customize it to frame your needs and your culture,” said Sedgwick. “You can choose from various tools and reports, connect with other systems via APIs, and automate workflows that reduce the workload.”
This customization made it easier for maintenance teams at each facility to share knowledge and resources, and for HCA leaders to build on and leverage the strengths of each plant to achieve new levels of operational control, efficiency, and effectiveness. Below are just a few of the specific ways eMaint CMMS has benefitted HCA.
- KPI Tracking Drives Down Downtime: Using eMaint, HCA has gained a clearer understanding of the factors that cause equipment failures or breakdowns. “We can now identify failure modes and root causes,” said Sedgwick. “That alone has helped us reduce downtime.”
The ability to easily track standardized metrics across all the facilities has also made a big difference. This comprehensive view of the entire asset landscape has allowed HCA to identify opportunities for improving Maintenance, Repair, and Operations (MRO) decisions. Leaders can now share consistent feedback with facilities, helping them target problem areas and improve performance across the board.Furthermore, HCA has implemented audits to ensure each site is following best practices for using eMaint. “Our maintenance excellence audits allow us to run specific reports to spot-check a site’s performance and its utilization of the system,” said Sedgwick. For example, HCA has built queries that can quickly determine the entirety of a site’s records. This audit process itself is standardized and systematized so that each site is evaluated in the same way.Such system-wide KPI tracking has led to significant improvements, reflected in data from audit reporting, capital expenditures, and Overall Equipment Effectiveness (OEE) measurements. - Real-Time Co-ordination with eMaint MX mobile version: This powerful tool improves maintenance management by providing mobile access to work requests, work orders, inspection rounds, parts inventory, asset tracking, and meter readings. It helps the maintenance team save time, reduce paperwork, and improve overall efficiency. “The ability to add detail with minimal to no additional time required really allows us to be very efficient on what we do,” said Sedgwick, which contributes to reduced downtime.
- Knowledge and Spare Parts Sharing: HCA has also saved time and money by tapping into eMaint’s data-based insights and by sharing resources across the facilities. A failure mode library, for example, lets teams document failure modes and use solutions that have worked before.
“If a site is struggling with a specific piece of equipment,” said Sedgwick, “we can reference a different site that functions efficiently in the same area. This allows for best practices on preventive maintenance activities, so the company does not have to reinvent the wheel every time.”
eMaint’s ability to streamline inventory management across multiple sites has also helped. With this system, HCA can quickly check if there’s a spare part in Ohio that could be useful at a site in California — visibility that is crucial when sourcing specialized spare parts or parts with extended lead times. - Integration-Driven Efficiency: HEXPOL integrates eMaint with SAP for their purchase order management. “eMaint is not just a cookie cutter system,” Sedgwick said. “It can be customized to fit your needs, so I think that’s one valuable aspect of it.” Connecting a CMMS to their other critical business functions helps HCA get the most out of every tool. In addition, syncing data between systems ensures that different business areas can work together effectively and have the current and, most up‑to‑date information.
Looking ahead, HCA plans to also use eMaint for condition monitoring and automation. With these tools, the company will unlock even greater output and value across its operations, building on the gains already made with the CMMS.
OUTLOOK
Using eMaint, Watco has saved a significant amount of time and improved their processes in multiple areas—from ensuring compliance and streamlining reporting to automating preventive maintenance tasks and getting ahead of potential issues.
eMaint is quickly becoming the go-to place for teams to find the information they need. “We use eMaint as the centralized database for all of our assets and asset detail,” says Prestholt.
“By using eMaint, we have been able to implement a large number of preventive and predictive maintenance standards, which greatly assists us when it comes to meeting the exact requirements of the automotive industry.“
– John Sedgwick, Director of Engineering and Maintenance, HEXPOL Compounding Americas