What is Maintenance Management?
Maintenance management refers to the coordinated activities of preserving and restoring equipment, infrastructure, and systems to ensure optimal performance and reliability. This discipline focuses on extending asset life, minimizing downtime, and managing maintenance costs efficiently, contributing to overall operational effectiveness.
What is Equipment Maintenance?
Equipment maintenance management is a strategic approach focused on the regular upkeep and optimal functioning of physical assets within an organization. This practice entails systematic planning, implementation, and monitoring of maintenance activities to ensure asset longevity, prevent malfunctions, and support seamless operational workflows.
Types of Maintenance Strategy
The right maintenance strategy can keep your plant running at optimal capacity while reducing your overall costs. Implementing the right maintenance approach will also help you standardize workflows and maximize your labor force. A CMMS can help you plan, track, and evaluate the success of your existing maintenance strategy.
Let’s take a look at four key types of equipment maintenance.
Preventive maintenance, also known as time-based maintenance, uses a schedule of maintenance tasks and routine inspections to ensure that machines are always in good working order.
Condition-based maintenance uses a network of sensors to continuously collect asset health data. Changes in asset vibration levels, temperature, oil quality, and other factors can indicate new asset faults. Condition monitoring lets teams spot potential defects early and address them immediately.
Predictive maintenance is a type of condition-based maintenance. Predictive maintenance uses condition monitoring data, along with analytic software, to make predictions about when machines are likely to need maintenance. Predictive maintenance lets teams stay ahead of problems and make smart scheduling decisions.
Run-to-failure maintenance is the practice of performing maintenance only when assets have broken down. This approach can work for less important assets — for example, most facilities let their lightbulbs run to failure. But when it’s applied to critical assets, it can result in expensive downtime and costly repairs.
What is the Best Maintenance Strategy?
The best maintenance strategy will increase operational efficiency, reduce downtime, and lower maintenance costs. But every facility’s strategy will be different. In fact, most facilities use several different maintenance strategies simultaneously because different assets have different needs.
In general, it’s a good idea to incorporate proactive maintenance approaches — like predictive maintenance and preventive maintenance — to keep your most critical assets in optimal working condition.
Performing an asset criticality analysis can also help you determine which assets are most important to your operation. This can drive decisions about the right maintenance strategy for each asset.
Elements of Maintenance Management
Maintenance management has four key elements: budgeting, scheduling tasks, regulatory compliance, and workflow optimization. Here’s what that looks like in action.
Budgeting is the practice of choosing how to use limited resources to keep assets up and running. It’s essential to balance the cost of maintenance against the cost of unplanned downtime caused by smaller problems that spiral out of control without necessary repairs or part replacements. A CMMS like eMaint can help managers track spending and generate detailed, granular reports.
Scheduling tasks is a constant challenge for any team dealing with labor constraints or a lean budget. Effective scheduling must consider the need for preventive maintenance tasks and emergency repairs. A good CMMS can help automate scheduling tasks and update schedules when maintenance needs shift or when your crew’s availability changes.
Complying with safety and quality standards that change quickly, from one year to the next, is difficult. A good maintenance strategy includes a detailed procedure for maintaining compliance and keeping records. A CMMS like eMaint can help by automatically storing work order and PM competition records in an easily searchable, central location.
Workflow optimization. There is always room for improvement when establishing workflows and procedures. The goal is to minimize setbacks that result from a lack of coordination and to conduct frequent inspections of machines to estimate the production rate. A CMMS can help standardize workflows by building detailed checklists into your work orders.
There is always room for improvement when establishing workflows and procedures. What’s important is figuring out which tasks are urgent and who should perform them. The goal is to minimize setbacks resulting from a lack of coordination and conduct frequent inspections of machines to estimate the production rate. Adding modifications can further enhance the reliability of heavy-duty assets.
What Is a Maintenance Checklist?
Maintenance checklists help ensure that maintenance tasks are performed correctly and in the right order, every time. Checklists are also a great way to standardize workflows and increase operational efficiency.
A robust checklist should include the precise steps needed to complete each task, along with any relevant information. eMaint can build checklists directly into your work orders so teams can access them anytime. Workers in the field can then use eMaint’s mobile app to read, update, and check off items on the list — all while on the go.
What Is the Goal of Maintenance Management?
Maintenance management has several important goals, including:
- Reducing asset downtime and increasing productivity
- Extending asset lifespan
- Reducing maintenance costs
- Increasing operational efficiency
- Maintaining regulatory compliance
An effective maintenance management program helps decision-makers analyze their existing processes and find room for improvement. That’s why a powerful, easy-to-use CMMS is crucial to the success of any maintenance management program.
A CMMS like eMaint lets you analyze costs, track maintenance KPIs, achieve regulatory compliance, and manage asset health. The result is a streamlined, efficient operation with significantly less downtime and greater productivity.
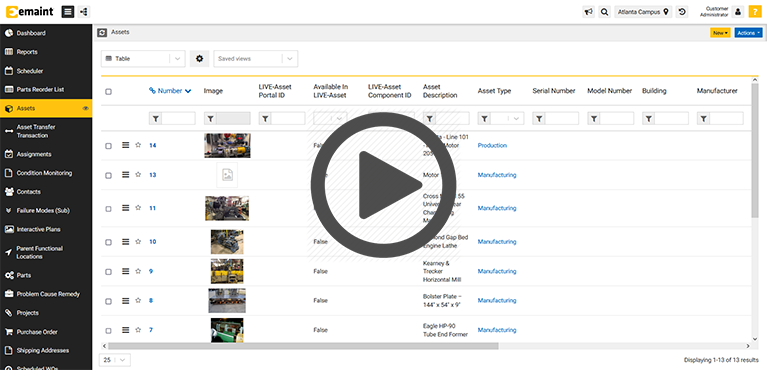
[/fusion_modal_text_link]
Best Practices for Managing a Maintenance Team
As a plant manager, you should be proactive about communicating with your team by being open to feedback and suggestions on how to improve existing processes. Before approving a request, it would be best to practice testing scenarios modeled after types of failure.
Your written documentation should be stored on a CMMS, describing the policies, procedures, user guides, and hierarchical flows of mechanical systems. Continuous improvement is the main objective, which means planning maintenance around the availability of machines.
The core principles of maintenance management are:
- Leadership
- Foundations
- Processes
- Improvement
- Results
Be able to define the scope of work before you try to gather the results. Run a cost-benefit analysis based on past outcomes to understand what the implementation challenges are. The final takeaway should be: What results are actually meaningful, followed by what are some resources to address these obstacles?
The truth is, a lot of time and effort goes into maintaining top-priority assets, so it makes sense to shoot for higher-quality performance while limiting the time and money spent to a reasonable amount. With an actionable plan, your team won’t be held back by unpredictable events anymore.
What is Maintenance Management Software?
Maintenance management software, also sometimes known as a computerized maintenance management system (CMMS), is a software that centralizes all of your maintenance information and provides tools to optimize asset performance. The goal of any maintenance management software is to increase the availability, utilization, and reliability of your equipment.
At the most basic level, maintenance management software is a complete solution for maintaining physical assets across your facilities. A CMMS enables you to effectively manage, automate, and streamline your maintenance operations.
Today, maintenance management software is increasingly cloud-based, rather than on-premise. This means that maintenance information is quickly accessible from any device, providing rapid visibility into all of your maintenance operations, even across multiple facilities.
Top Features of Maintenance Management Software
Maintenance management software solutions offer a wide variety of features and capabilities, including:
- Preventive maintenance management and automation
- Centralized asset management throughout the entire asset lifecycle
- Work order management and automation
- Inventory management, tracking, and automated re-ordering of parts
- Condition monitoring and analysis for predictive maintenance and prescriptive maintenance.
- Reporting & analytics dashboards
- Digital record-keeping for audit preparedness
- Safety & compliance management
A maintenance management software with an intuitive user interface makes it seamless for users of any level to access the information and tools they need to do their jobs more efficiently.
What are the Benefits of Maintenance Management Software?
There are many advantages to leveraging a maintenance management software, or CMMS, in your maintenance operations.

Centralizes Maintenance Information
Clear and effective communication throughout your organization is critical. A CMMS provides a single source of truth for all of your maintenance activities and related information. This reduces the risk of miscommunication, so decisions are made based on the most up-to-date and accurate information possible while keeping maintenance teams on the same page with their maintenance program.
Increases Asset Uptime While Reducing Costs
By helping maintenance teams fine-tune their operations, a maintenance management software can increase the effectiveness of your maintenance program. For example, a CMMS aggregates critical condition monitoring data and issues alerts when a potential problem is detected. This enables maintenance teams to respond promptly when and where they are needed more. Ultimately, by enabling more proactive maintenance approaches, like predictive maintenance, maintenance management software reduces costly unplanned downtime and reduces overall maintenance costs.
Streamlines Work Order Management for More Efficient Workflows
Management and automation of work orders is the key capability of any asset management software. This reduces the risk of errors due to manual work order management, while increasing efficiency by making it easy for technicians to see what needs to be done.
Digitizes and Automates Record-Keeping for Compliance and Audits
A CMMS solution can often replace manual paper filing and spreadsheets, making it easier to stay organized and properly maintain all of the necessary documentation in the event of an audit. For example, a maintenance management software can be used to automatically log information about every asset in your facility in a centralized location. In case of an audit, this digital record can easily be exported into a file or report. This not only ensures compliance with relevant standards but can also facilitate faster audits and avoid downtime for investigations.
Choosing the Best CMMS Software / Maintenance Management Software
When selecting a maintenance management software, it’s important to consider not just features and capabilities. It’s also important to consider whether the vendor offers the level of support you need to execute the solution effectively within your organization. For example, in addition to its core capabilities, the technology should also be expandable to include other maintenance functions, such as vibration sensors or other online condition monitoring techniques.
Maintenance management solution providers should also provide robust training and support services before, during, and after software deployment to help reduce the adoption curve and enable continuous improvement of the installed system.
It is also important to ensure that legacy systems can be integrated into newer software to protect the integrity of the databases—and save time and frustration of working with incompatible systems.
Why Your Team Needs Maintenance Management Software
Maintenance management software is designed to give you a clear picture of trending data on critical infrastructure across many locations.
One benefit is condition monitoring in real-time, which lets organizations make data-driven decisions to cut down costs and increase their overall uptime. This eliminates many time-consuming manual processes, so you can plan accordingly for downtime with increased visibility on scheduled work orders.
From the dashboard, there are features like tracking the MRO inventory so you know what items to purchase for replacing damaged parts. Auditing capabilities make it possible to stay up-to-date on the latest SOPs, allowing you to create a maintenance history on any asset with timestamped photos and certifications.
There are many efficiency and lifecycle benefits from implementing and using computerized maintenance management system software. Overall, it allows teams to align their maintenance practices and activities with other departments and business goals. When you have a system that allows cross-departmental data sharing, everyone’s job gets a little more efficient.
Installing a CMMS is one solution that lends greater visibility to your facility environment. Some of them even support integrations with accounting software or project management apps to help boost employee productivity and ensure that all core functions are transparent.