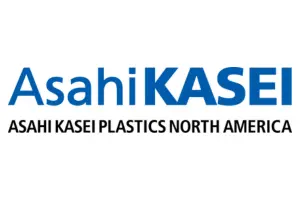
Asahi Kasei Plastics North America Hits 97% On-Time PM Completion Rate with eMaint X5
The automotive plastics manufacturer moved seamlessly to eMaint X5 and now uses reports and dashboards to track performance across multiple sites.
Customer Since: 2012 | Industry: Automotive
Asahi Kasei Plastics North America ( APNA ), an automotive plastics manufacturer, continuously works to improve its preventive maintenance program. A decade ago, the company realized its paper-based approach was hampering its ability to reach its targets as effectively as possible.
In response, they implemented eMaint Computerized Maintenance Management System (CMMS) to better track and manage preventive maintenance tasks. Now, with eMaint X5 and a PowerBI integration, APNA has unlocked automated data syncing and real-time performance monitoring, giving the team immediate access to critical metrics and the ability to respond proactively to emerging issues.
The result? A 97% on-time Preventive Maintenance (PM) completion rate — surpassing their original KPI target — and improved maintenance efficiency across two facilities. Plus, with more time and better insights now at their fingertips, the maintenance management team is able to keep the company laser-focused on continual improvement.
BACKGROUND
Headquartered in Fowlerville, Michigan, Asahi Kasei Plastics North America is a plastics compounder that manufactures high-performance plastic pellets for automotive manufacturing, healthcare, and other industries. Most cars on the road feature Asahi Kasei plastic.
The company began using eMaint more than 10 years ago, shifting from paper to a CMMS to better track preventive maintenance activities, add on-time completion metrics, and improve data accuracy.
CHALLENGES
Holly Trpik, Maintenance and Reliability Manager, highlights the key issues that prompted APNA to turn to eMaint:
- Manual and time-intensive maintenance tracking: “Previously, we tracked most of our PMs on paper. Those were printed weekly, had instructions, and were signed off,” said Trpik. However, given that the team manages 1,500 assets and 10 production lines in the Fowlerville, Michigan facility alone, the manual process was overwhelmingly inadequate for the scale of the operation.
- Improving on-time PM completion rate: Historically, the team only tracked whether PMs were completed, not when they were finished. This lack of detail made it difficult to identify and address patterns of delay, directly impacting the company’s goal of reaching a 95% on-time PM completion rate.
- Coordinating spare parts across facilities: Managing spare parts at just one facility is already a balancing act. But without a system linking Asahi Kasei Plastics North America’s two facilities — one in Michigan and the other in Alabama — it was nearly impossible to determine if a spare part needed urgently at one site was sitting unused at the other. Such gaps in visibility and the lack of connection between facilities often made timely repairs much more challenging.
IMPLEMENTATION
Trpik led the migration to eMaint X5 in 2022 — a move that was a key part of her duties as CMMS administrator, which included managing work requests, PM schedules, and semi-annual shutdowns.
An important part of the eMaint implementation for her was setting up an integration with PowerBI, a data analytics reporting tool developed by Microsoft. “Our central IT department worked directly with the eMaint team,” said Trpik. “Together, they built the backend structure that allowed us to connect with PowerBI and decide which data entities and fields we wanted to be reported into the SQL database.”
This implementation and integration marked a turning point, equipping the team with measurable and significant improvements.
RESULTS
Post-implementation, the advantages of the new eMaint and PowerBI system quickly became evident.
- 97% on-time PM completion rate: With eMaint X5, the Asahi Kasei Plastics North America team implemented an on-time metric as a bonus for technicians and used the CMMS to stay on track with their preventive maintenance tasks. This led to immediate improvement, with the team quickly achieving a 95% completion rate — their original goal. Then, eMaint’s integration with PowerBI unlocked further real-time data visibility, helping push the completion rate up to an impressive 97%.“Before the integration … it took me two days to collect all the data, so it was a lagging indicator,” said Trpik. “Now, the PM completion data is automatically pulled into a PowerBI dashboard,” enabling individuals and the whole team to see real-time data so they can immediately act upon it.
- Streamlined and coordinated maintenance across sites: APNA’s plant support equipment consists of critical assets that service multiple lines. So, if a critical asset breaks down, multiple lines must be stopped. With the switch to eMaint X5, Trpik and her team streamlined the management and sharing of resources across the Michigan and Alabama plants to help prevent unplanned downtime.
- One PM library for both facilities: PMs are now mapped within the two plants, creating a cohesive maintenance strategy across the board. “It’s a lot easier to make an edit for one plant and then push it to the other plant now,” said Trpik.
- Spare parts at the ready — always: Sharing a spare parts inventory across both facilities means the team can quickly identify and dispatch necessary components, significantly speeding up the time it takes to complete repairs and reducing equipment downtime. “The CMMS lets us look at both sites and see if one site has something the other site needs,” said Trpik. “It’s helped us quite a bit with urgent repairs. We just send the part down or up to the other plant.”
- Automated data insights and reporting: The eMaint X5 integration with PowerBI has streamlined data handling, significantly reducing manual effort. “I basically automated myself out of a job at this point because something that took me two days five years ago now takes no time at all,” said Trpik. “I just have to go to my PowerBI report and it’s there.”This newfound efficiency has freed up significant time for her, allowing Trpik to focus on further improvements and strategic projects within the company.
“My favorite aspect of eMaint is its ability to streamline automation and tracking. And the customer support team is exceptional; they’re not just helpful — they’re partners. If I need a functionality that isn’t available, I reach out, and they’re proactive about developing solutions because it might not only help me, but also help other customers. I really appreciate the ongoing commitment to continuous improvement. It feels like a true investment in our success.“
– Holly Trpik, Maintenance and Reliability Manager, Asahi Kasei Plastics North America