Maintenance key performance indicators (KPIs) evaluate factors critical to an organization’s success. They are used to measure performance against goals related to machine failures, repair times, maintenance backlogs, and costs.
One of the best ways to track maintenance KPIs is by using Computerized Maintenance Management Software (CMMS). With a CMMS, users can develop baselines that measure and expose opportunities for improvement. Using a CMMS can make the difference between organizations achieving or failing to meet their maintenance KPIs.
What is a Maintenance KPI?
A maintenance KPI, or Key Performance Indicator, is a benchmark for measuring the performance of maintenance personnel or teams in achieving their goals. Maintenance KPIs are specific targets, like “decrease downtime by 25%,” for tracking progress in accomplishing bigger goals like preventing downtime, reducing costs, or strengthening machine reliability. A KPI is the combination of a metric, like downtime, and a benchmark, like a decrease of 25%, that quantifies success for a goal, like preventing downtime.
Establishing maintenance KPIs makes your goals measurable and gives you quick insight into project progress. A good KPI is true to the SMART acronym of Specific, Measurable, Achievable, Realistic, and Timely.
Maintenance leaders rely on KPIs as proof their teams are hitting the mark – or insight into why they’re not.
What is a Maintenance Metric?
A maintenance metric is any datapoint an organization tracks, from uptime to overtime hours worked. Metrics are measurements that can be used to track success with KPI benchmarks, quantify task progress, monitor for potential failures, and much more.
Maintenance metrics track the employees, machines, operations, and inventory that influence whether you reach your goals. Common maintenance metrics include Mean Time to Repair (MTTR), Mean Time Between Failures (MTBF), and Overall Equipment Effectiveness (OEEE).
Successful maintenance teams analyze which metrics are the true indicators of their success, and which metrics are better thought of as just contributors to success or should be ignored altogether.
Maintenance KPIs vs. Maintenance Performance Metrics
Maintenance KPIs are targets or benchmarks that indicate goal success, whereas maintenance metrics are the data points these targets are based on. Let’s say you have a goal to strengthen an asset’s reliability. You may determine that uptime is the best metric to track for your goal, and so set your team a KPI of increasing uptime by 15% in the next year.
Simply put, maintenance KPIs track an organization’s success at meeting its goals. Are you cutting costs and reducing downtime? KPIs offer the ground truth on your journey toward continuous improvement. As the saying goes, “Measure What You Treasure.”
There are a few different categories of maintenance KPIs such as, leading and lagging indicators. A leading indicator signals future events and includes metrics like Preventative Maintenance Compliance or Estimate vs. Actual Performance. Lagging indicators include maintenance metrics like Mean Time Between Failure (MTBF) and Mean Time to Repair (MTTR). The most comprehensive CMMS KPI tracking includes a mix of both leading and lagging indicators.
Some common examples of maintenance goals around which metrics and KPIs focus include:
- Reducing Costs
- Reducing Failures
- Reducing Downtime
- Increasing Work Identification
- Increasing Work Planning
- More Effective Work Scheduling
- More Effective Work Execution
A CMMS offers an elite process for tracking maintenance performance metrics and transforming metric and KPI data into meaningful reports and dashboards. As a result, organizations gain both quantitative and qualitative insight. Quantitively, our system gives businesses the ability to see their performance compared to their goals. Qualitatively, a business can see how their performance compares to current competitors in the “world-class maintenance” category.

How to Track Maintenance KPIs with eMaint CMMS
Within eMaint CMMS, organizations can set and measure KPIs ranging from the productivity of an individual to the overall performance against budget across an entire department. The information that matters for maintenance goals is different for every company, so it’s important to use the top-down planning method to understand how every aspect of the business affects reaching the goals set.
The CMMS organizes and presents the most relative and important information in a way that makes your next action steps clear in one space. When you purchase eMaint CMMS, you also gain a designated customer success manager to help with setup and answering questions.
Below are a few examples showing how a company can leverage eMaint’s work management and reporting tools to monitor maintenance KPIs.
XTO Energy, a producer of natural gas in the United States, was looking for a CMMS because their former hand-written system resulted in misplaced or unattended work requests. With eMaint, the company saw an increase from 70% to 100% in work completion rates with no additional staffing. They also always gained visibility of the work backlog.
Klein Plastics produces plastic products for manufacturers and major suppliers of automotive parts, appliances, hand tools, and office furniture. After implementing eMaint, Klein Plastics saw benefits of the system including a 20% increase in overall Equipment Effectiveness, and an improvement in consistency, communication, and productivity.
Develop Maintenance KPIs with SMART Goals
It’s important to implement maintenance KPIs with intention. That’s why good CMMS uses S.M.A.R.T. goals (specific, measurable, achievable, realistic, and timely). These terms are important factors to consider when ensuring goals are met.
So, ask yourself: “Are my maintenance goals S.M.A.R.T.?”
Now, look through the terms as they apply to maintenance KPIs.
Specific: What are the 5 W’s of the goal? (Who, What, When, Where, Why) |
Measurable: What are the measurable and essential components of the goal? |
Achievable: Have you or a competitor attained this goal in the past? |
Realistic: Is reaching your goal practical in your current state? |
Timely: Did you map out the time it will take to obtain your goal? |
Important Examples of Maintenance KPI Metrics to Benchmark and Track
A Computerized Maintenance Management System (CMMS) tracks and uses maintenance KPIs to establish, benchmark, and monitor all parts of an organization’s goal. That’s why CMMS users experience visible improvements in many areas, including:
Maintenance Backlog
Maintenance backlogs are an accumulation of maintenance work that shows what needs to be dealt with based on safety issues or to prevent breakdowns. This KPI is important because the longer work is not completed, the greater the risk of more serious and costly failures.
The goal is to control backlog during normal operations and in emergencies. Neglecting to track this maintenance KPI creates a lack of visibility into the backlog. This can result in staffing challenges, firefighting, and a lack of work prioritization.

Mean Time To Repair (MTTR)
Mean Time To Repair is a basic measure of the maintainability of repairable items. It represents how long a piece of equipment is out of production, or the average time required to repair a failed component or device.
MTTR Calculation = Sum of Downtime Periods ÷ Number of Downtime Periods = MTTR
MTTR can have a significant impact on the bottom line of an organization and can mean missed orders and missing business objectives. By tracking and monitoring this data, organizations can get a better understanding of necessary staffing, inventory management, and repair vs. replace decisions based on data. It also introduces a method to understand how well an organization responds to repairs and equipment problems.
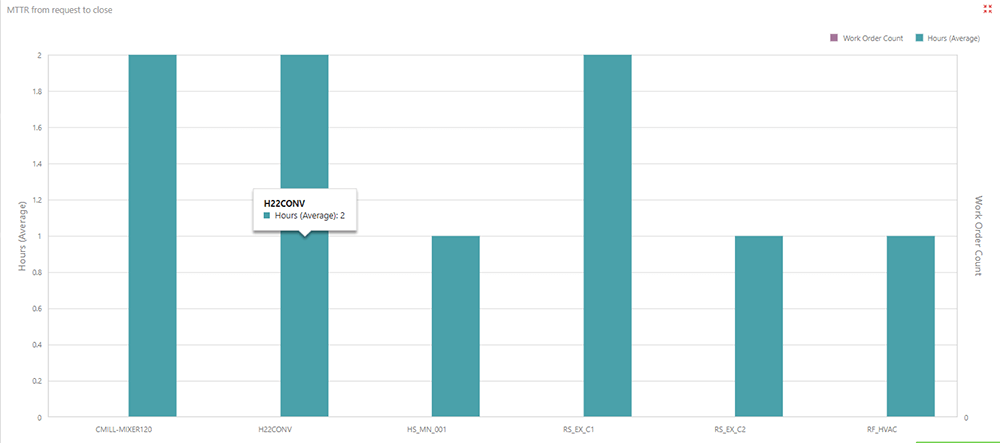
Mean Time Between Failures (MTBF)
Mean Time Between Failures is the elapsed time between failures of a system during operation. For critical pieces of equipment, MTBF is an important way to discern the performance of an asset.
MTBF Calculation = Sum of (Start of Downtime – Start of Uptime)
Number of Failures
MTBF is an important way to quantify the reliability of an asset and predict future performance. Organizations can optimize their preventative maintenance schedules by carefully tracking this KPI and associated performance metrics like downtime, uptime, and the number of failures. Organizations can leverage MTBF to determine preventive maintenance tasks such as rate of inspections or introduce preventive actions such as lubrication, greasing, and calibrations. This can help to avoid unexpected failures and reduce the risk of performing unneeded maintenance on a piece of equipment.
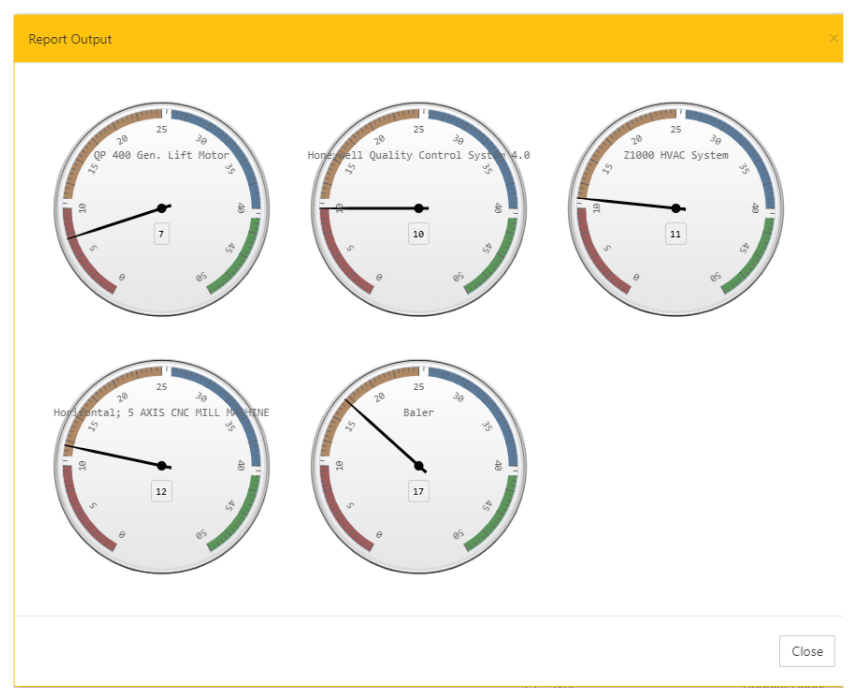
Overall Equipment Effectiveness (OEE)
Overall Equipment Effectiveness evaluates how effectively a piece of equipment is utilized. The OEE calculation is based on the three OEE Factors:
- Availability = Run Time / Planned Production Time
- Performance = (Ideal Cycle Time × Total Count) / Run Time
- Quality = Good Count / Total Count
To discover the total OEE for a particular piece of equipment:
OEE = Availability x Performance x Quality
OEE provides an informed, data-driven picture of how effectively your maintenance processes are running based on critical factors such as availability, performance, and quality of equipment. With a CMMS, it is easy to track improvements over time.
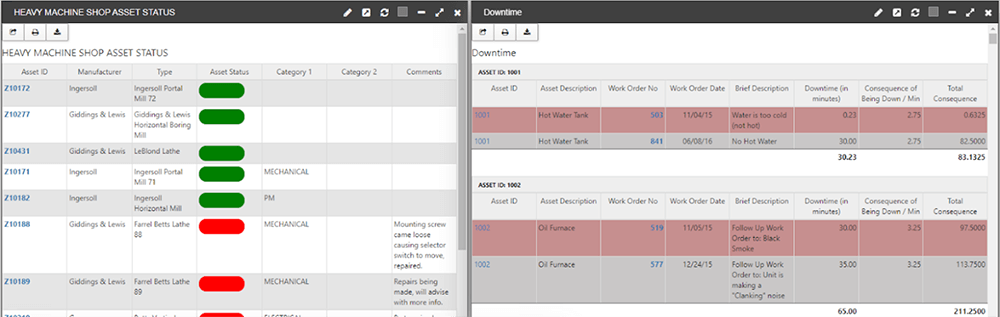
Preventive Maintenance (PM) Compliance
Preventive Maintenance is work that is performed on a piece of equipment on a predetermined schedulebased on elapsed time or usage — to lessen the likelihood of it failing. Preventive maintenance is performed while the equipment is still operational so that it does not break down unexpectedly. PM Compliance is the percentage of scheduled preventive work orders that are completed with a predetermined time.
A good rule of thumb for PM Compliance is the 10% rule. This means that PM tasks should be completed within 10% of the scheduled maintenance interval. Monthly PMs should be completed within 3 days of the due date. These measurements can give organizations a more nuanced understanding of whether or not a PM program is effective.
Organizations can create reports based on compliance to offer data-driven proof of this effectiveness. They can also create and a line of sight into issues impacting your maintenance program.
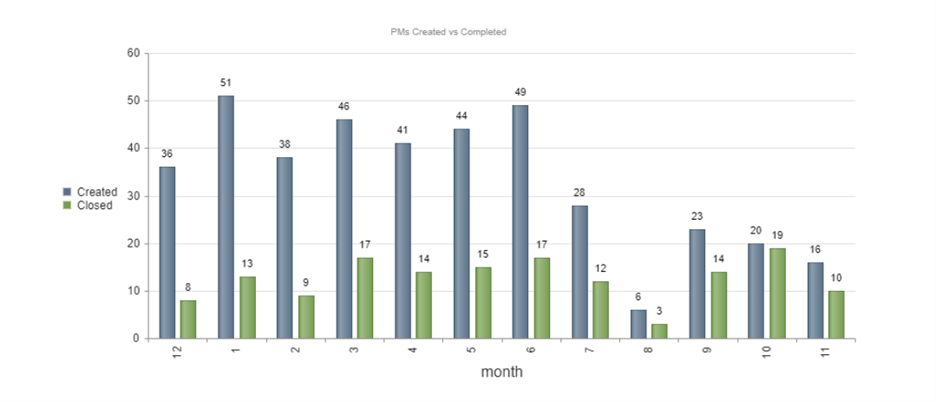
Planned Maintenance Percentage
Planned Maintenance Percentage is the percentage of maintenance hours spent on planned maintenance activities versus unplanned. This percentage can be found by dividing the scheduled maintenance labor hours into the total maintenance hours during a particular period.
“World-class maintenance” suggests that 90% of maintenance should be planned. However, an 80% planned to 20% unplanned ratio is still considered beneficial compared to the typical average of 55% or less. Planned Maintenance Percentages can be easily tracked with an effective CMMS.
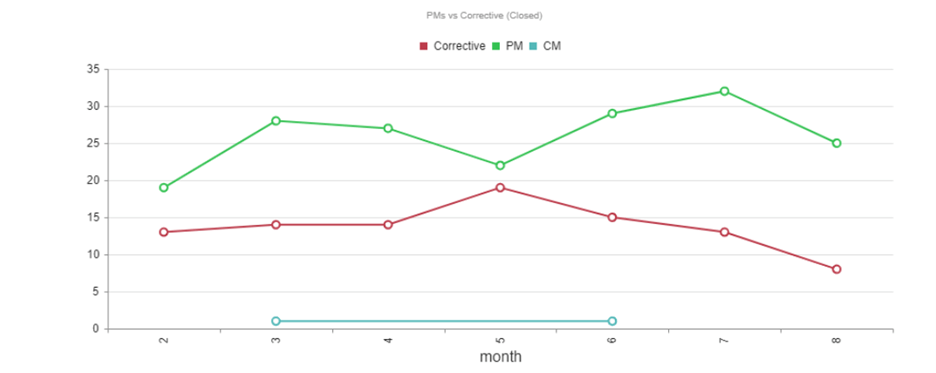
What are the Leading Maintenance KPIs?
Maintenance performance indicators are metrics used to evaluate the effectiveness and efficiency of maintenance activities within an organization. These indicators, including MTBF (Mean Time Between Failures), MTTR (Mean Time To Repair), system availability, and maintenance costs, provide essential insights into the reliability and operational readiness of assets, guiding strategic decision-making and improvements in maintenance practices.
The primary maintenance Key Performance Indicators (KPIs) are critical metrics that help organizations track the efficiency and effectiveness of their maintenance operations. These include:
- Mean Time Between Failures (MTBF): This indicator measures the average time between system failures, helping to assess the reliability of assets.
- Mean Time To Repair (MTTR): This measures the average time taken to repair failed equipment, indicating the efficiency of the maintenance team.
- Availability: Calculates the percentage of time that equipment is operational and available for use, reflecting the overall effectiveness of maintenance processes.
- Reliability: Assesses the probability that a machine or system will perform its intended function adequately for a specified period under typical conditions.
- Maintenance Backlog: Quantifies the maintenance work that has been identified but not yet completed, providing insight into the potential future workload.
- Machine Downtime: Tracks the time equipment is not operational due to breakdowns or maintenance, directly impacting productivity.
- Maintenance Cost as a Percentage of Estimated Replacement Value (MC/ERV): This metric compares the annual maintenance cost to the replacement value of the assets, helping to gauge the financial efficiency of maintenance expenditures.
- Distribution by Types of Maintenance: Break down maintenance activities by type, such as preventive, predictive, and corrective, allowing for analysis of maintenance strategies and their effectiveness.
These KPIs enable maintenance professionals to identify areas for improvement, optimize maintenance schedules, and ultimately increase the longevity and performance of their equipment.