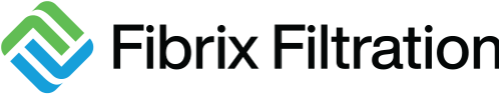
Fibrix Filtration Achieves 90% Work Order Completion Rate in First Year with eMaint
Customer Since: 2022 | Industry: Manufacturing
See how Fibrix Filtration focused on equipment reliability and shaped a forward-looking company vision based on real-time data provided by eMaint CMMS.
Summary
Fibrix Filtration, a prominent player in the production of non-woven textiles, faced the challenge of overhauling its maintenance operations to enhance efficiency and data-driven decision-making.
With the goal of shifting from a reactive to a proactive maintenance strategy, Fibrix Filtration embraced eMaint Computerized Maintenance Management System (CMMS) in 2022. Within a year, they saw their work order completion rate soar to more than 90%.
- Preventive Maintenance (PM) and work order completion rate hit 90+% in the first year
- Successfully shifted focus from reactive maintenance to equipment reliability
- Leveraged improved data collection to create a company-wide vision of the future
- Optimized spare parts inventory and simplified inventory purchasing process
BACKGROUND
Fibrix Filtration, formerly known as HDK Industries, is one of the premier leaders in making non-woven textile products. It has five facilities and delivers a wide range of innovative solutions to local, national, and regional companies in industries such as HVAC, paint collection, liquid, evaporative cooling, and specialty filters.
“If you buy air filters residentially or commercially, more than likely the filter media in those air filters is going to be some of the product we make in our factory,” said Scott Hammitt, Fibrix Maintenance Reliability Engineer.
Fibrix Filtration has been an eMaint customer since 2022.
CHALLENGES
Prior to working with eMaint, Fibrix Filtration didn’t have any type of CMMS. The company was using a Microsoft Excel spreadsheet tied to its ISO certification to carry out preventive maintenance. “It was a system that worked, and they were able to do preventive maintenance, but there was just no structure, and no organization based on good data and good vision,” Hammitt said.
Hammitt joined the Fibrix team after working for over 15 years with eMaint in his previous role at a sister company. At Fibrix, he was asked to establish a more structured and organized maintenance program and to focus on maintenance and reliability for all the equipment plant-wide. He chose to implement eMaint to facilitate the project.
“When I came in, setting up eMaint X4 was one thing that I really wanted to do from the ground up,” Hammitt said. “That was the main thing: Focus on how to change the culture and make sure everybody has buy-in to what we are trying to accomplish with the platform.”
IMPLEMENTATION
Since Fibrix had never used a CMMS system before, implementing eMaint involved training the team on new processes and creating a cultural shift across the organization. Fibrix also implemented Fluke Mobile so technicians could easily access data and records while in the field.
“We used eMaint University and some tutorials to get the guys trained,” explained Hammitt. Once we started using Fluke Mobile, it was very user-friendly. We trained our technicians and managers involved in the program.”
Even though the maintenance team had never seen a CMMS system before, it only took a few weeks to get trained and comfortable using the software. Now, they use it daily on the job to complete work orders and preventive maintenance, track labor hours, and much more.
RESULTS
Because Fibrix was not used to using a CMMS, Hammitt implemented only a few basic goals for the first year. He hoped the company could reach a 75% preventive maintenance completion rate and an 85% work order completion rate. By the end of the year, Fibrix was over 90% for both metrics – and Hammitt credits eMaint for helping them get there.
“The data reflected how, now that we have a vision, we can see exactly what can be accomplished with eMaint. We have a better vision around the real-time data that’s being collected,” said Hammitt. “With that, we’re able to focus on the reliability of the equipment tied to every work order.”
Fibrix also uses eMaint to make all maintenance purchases, as well as for inventory optimization. The company has found that effective parts inventory management software makes it easy to see which parts are available and reduces unnecessary costs and wasted time associated with searching storerooms for parts.
eMaint’s data collection and reporting features make it simple to see what’s happening in real time, allowing for informed decision making about asset replacements, inventory management, KPIs, and more.
“A lot of times, we were making decisions related to data that wasn’t really available. They were more like guesstimates,” Hammitt said.“But with eMaint, going forward, we’re going to have better vision and data, and we’re making better decisions because of that.”
“eMaint has provided a better platform and a better way to be able to make better decisions going forward.”
– Scott Hammitt, Maintenance Reliability Engineer