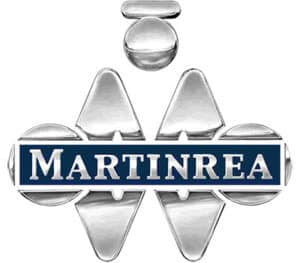
Martinrea Metallics: Standardization across plants and 95%+ on-time completion rates using eMaint CMMS software
Customer Since: 2017 | Automotive
Manufacturers in the automotive industry experience some of the costliest equipment downtime of any industry. In a survey of 101 manufacturing executives ─ from part suppliers to engine makers to automakers ─ the majority of respondents stated that downtime costs their company an average of $22,000 per minute.
Martinrea Metallics, a Tier One automotive parts manufacturer, supplies parts to BMW, Nissan, Chrysler, Fiat, Ford, and General Motors. Martinrea wanted CMMS software that would enable it to standardize maintenance at its 12 North American plants. The company chose the eMaint CMMS because of its proven ability to support multi-plant operations and world-class maintenance goals.
BACKGROUND
Martinrea is a diversified global automotive supplier engaged in the design, development, and manufacturing of highly engineered, value-added Lightweight Structures and Propulsion Systems. The company designs, develops and manufactures metal parts, assemblies, and modules, complex fluid management systems, and aluminum products for the automotive industry. The organization employs approximately 15,000 people in 47 operating divisions in Canada, the United States, Mexico, Brazil, Germany, Slovakia, Spain, and China.
Martinrea’s mission is to make people’s lives better by delivering outstanding quality products and services to its customers and by providing meaningful opportunities, job satisfaction, and job security for its employees.
THE CHALLENGE
When Brent, Technical Group Manager for Martinrea Metallics, took on the task of standardizing the company’s 12 North American plants, each entity was operating separately. Interaction between plants was nonexistent, and facilities were using a medley of computer maintenance management systems (CMMS). Catastrophic failure rates were at unacceptable levels, and maintenance costs weren’t being tracked accurately. The maintenance management practice, overall, was considered broken.
Martinrea’s goals included the unification and standardization of all plants, including capabilities, asset naming, codes, reporting, PMs, and CMMS software integration. The organization also wanted complete visibility and a consolidated view of all plant operations while striving for and maintaining world-class maintenance.
IMPLEMENTATION
Based on positive feedback from its Hopkinsville, Ky., plant, which had been testing eMaint for about a year, Martinrea Metallics leadership and Brent chose eMaint CMMS software. Martinrea implemented the eMaint enterprise-level, multi-site toolkit, and started using the system to build an international roadmap for its maintenance reliability program. The user-friendly toolkit allowed for reporting and data access across multiple locations.
Brent’s goals were ambitious, including wanting a 95%+ work completion rate systemwide. He started by evaluating each plant’s maintenance practices and tool usage. Using the system’s configurability capabilities, Brent developed rules to ensure:
- Individual plant accountability and mistake-proof PM workflows
- Compliance with internal predictive and preventative maintenance mandates
- Follow-up action on issues identified during third-party contractor audits
- Proper system usage and ongoing plant adherence to set standards
Brent established administrators and gatekeepers so that unauthorized changes could not be made to the standards. Within a matter of months, all sites were using the eMaint CMMS.
RESULTS
By using the eMaint CMMS pre-populated fields and categories functions, automatic workflows were developed to standardize and maximize PM processes and procedures and improve efficiency. Since the implementation, the organization has gained continuity between all divisions and can show stakeholders and customers a cohesive, interactive maintenance operations system.
“We had an audit done by BMW in our Hopkinsville facility after we started implementing eMaint across the other plants,” said Brent. “They described it as world-class. When you can sit a customer in front of a computer and basically show them your entire operation, they were very impressed.”
Leadership has systemwide visibility of the work in progress. Most plants continually meet or exceed the 95% work completion goal. Maintenance and reliability teams now make proactive maintenance decisions and have moved away from a firefighting mode and into a continuous improvement mode.
BENEFITS
“I really like the system. If we didn’t, we wouldn’t be moving it into our other groups. People are seeing benefits from it. We’re getting better at things. We’re getting better information. And the capabilities are seen by people and understood to be a benefit. What’s really been a big success for us is getting the information, [getting] what we need to know on how we’re operating.”
– Brent, Technical Group Manager for Martinrea Metallics