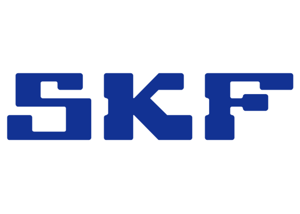
SKF Standardizes Maintenance Across 81 Facilities and 76,000+ Assets with eMaint
Customer Since: 2023 | Industry: Automotive
eMaint empowered bearing manufacturer SKF to standardize failure codes and improve technician productivity with a unified global CMMS platform.
SKF has standardized over 76,000 assets and 133,000 spare parts, significantly improving data visibility and efficiency.
Looking ahead, SKF plans to integrate eMaint with condition monitoring tools and AI for predictive maintenance.
- Global maintenance standardization across 81 facilities, 76,000 assets, and 133,000 spare parts – with plans to reach 200,000 assets and 1,000,000 spare parts
- Leveraged multi-language, multi-currency capabilities, streamlining work across countries
- Standardizing failure codes, assets, and spare parts to improve data accuracy across factories
- eMaint mobile app achieved significant savings on time and labor
SUMMARY
SKF, a global leader in bearing manufacturing, is implementing the eMaint multi-language CMMS across its 81 global factories to standardize maintenance processes and boost efficiency. Before switching to eMaint, SKF struggled with fragmented CMMS systems,
inconsistent asset naming conventions, and limited technician mobility.
By adopting eMaint as a unified platform, SKF factories can use a “Golden Master Template” to ensure consistent data, streamline reporting, and simplify future factory deployments. Technicians can access work orders and manage assets from their mobile devices,
reducing unnecessary trips and saving valuable time. eMaint multi-language support enables seamless adoption across global sites.
Although implementation is still in progress, SKF has already standardized over 76,000 assets and 133,000 spare parts, significantly improving data visibility and efficiency. Looking ahead, SKF plans to integrate eMaint with condition monitoring tools and AI for predictive maintenance.
BACKGROUND
SKF is one of the largest manufacturers of bearings in the world. Based in Sweden with sites in 129 Countries, it operates 81 global factories and produces some of the world’s most innovative friction-reducing products for a more energy-efficient future.
All 81 SKF factories are implementing eMaint to enable standardization, manage assets and work orders more effectively, and to improve maintenance technicians’ efficiency through mobile CMMS access.
CHALLENGES
Joachim Ruopp, Business Owner for CMMS Deployment, and Pablo Porcelana, SPS Reliability champion, outlined several of the challenges SKF faced which led them to eMaint.
- Lack of standardization: Many of SKF’s locations were already using a CMMS. However, the systems were not connected. Each factory had its own naming conventions for parts, assets, and failure codes, and updates to the CMMS had to be paid for and installed on a per-factory basis. Without standardization, it was impossible to run global reports to look for patterns or compare multiple facilities.
- Change management: Transitioning 81 locations to a unified system was a significantchallenge. eMaint needed to be integrated with other software used across SKF factories, and employees needed to be able to use it effectively to keep production and maintenance tasks on schedule. “One of the biggest goals we had was, how to make life easier for the maintenance technicians, for the maintenance planners, for the guys that are working in the frontline every day in maintaining our assets?” explained Porcelana.
- Lack of mobility for technicians: The previous CMMS lacked mobile capabilities. As a result, when technicians finished tasks, they had to return to the maintenance department to get the next work order, wasting valuable time and limiting their ability to perform repairs and maintenance tasks quickly.
IMPLEMENTATION
The eMaint team worked with SKF to develop a “Golden Master Template” to simplify and streamline rollout across its locations. The template includes all integrations, standards, and master data. “When we go to another factory, whether it’s the second or third or thirtieth, they all use the same template,” explained Ruopp.
And since it supports dozens of languages, technicians and operators could immediately begin using eMaint in their local language and currency, making the rollout seamless and enabling the global workforce to quickly adopt the CMMS without barriers.
RESULTS
Even though SKF’s transition to eMaint is still in progress, the SKF team has already seen significant benefits at 21 of its factories around the globe.
-
- Standardized naming of assets, failure codes, and spare parts: Regardless of location, every factory uses the same names and codes. “Now, we have the possibility to create standards around the world… Everybody has to use the same failure codes,” said Ruopp. “We have a naming convention for the machine description. It’s globally done. Every factory looks the same.”
- Improved search and data visibility: SKF manages around 76,000 assets and 133,000 spare parts with eMaint. “In eMaint, we can find every machine,” explained Ruopp. “We don’t have to look for the exact name, but we can search ‘grinder’ for example, and I can see all my machines that can grind. It’s really good.”
- Mobile capabilities: Every technician has a mobile device, enabling them to switch tasks quickly. Notifications tell working technicians when nearby assets need attention. “They don’t have to go back to the maintenance area and see what the next work order is,” said Ruopp. “They can do it directly on their phones. They can book the parts, they can open the work order, they can close the work order. They save a lot of time.”
- Localization with language and currency: eMaint translates into the local language and currency, eliminating potential barriers to use. “They don’t have to think about what something is called in English or another language,” Ruopp said. “They can do it in their local language.”
- Integration with key software: While SKF is still early on its eMaint adoption journey, some locations have already started using it for condition monitoring. The eMaint webbased SaaS platform with API integrations enables improved preventive and predictive maintenance capabilities. “eMaint has the possibility of taking data from our installed sensors and triggering work orders automatically,” said Porcelana. “We’re also thinking of integrating with GoPlant, Kardex, SAP, with different platforms that can give our maintenance teams even better results.”
SKF has implemented eMaint at 21 factories so far, but that number will scale quickly. “In the next two years, we will finish with all 81 factories,” said Ruopp. “That means we will have around 200,000 assets and a million spare parts in eMaint.”
While shifting all its factories to a unified CMMS is no small task, the SKF team has been continually impressed with eMaint support staff. When SKF presents eMaint with a new request or challenge, “They never tell me ‘That’s not possible,” said Ruopp. “Instead, they say, ‘Give us some time.” Ruopp and Porcelana speak with their customer success managers several times a week, and they are “always very responsive,” according to Porcelana.
Porcelana is particularly excited about utilizing AI for predictive maintenance with eMaint. “We have several projects running. Some projects are related to machine learning connected with AI to predict failures,” he said. “We also have projects related to a chatbot to support maintenance activities.”
“We think that these are two good ways to implement AI,” he said. “I think that is the future. And working together with eMaint and Fluke Reliability will be great.”
“Wanderson, our Customer Success Manager (CSM), is motivated 150%… I can call
him at midnight.“
– Joachim Ruopp, Business Owner for CMMS Deployment