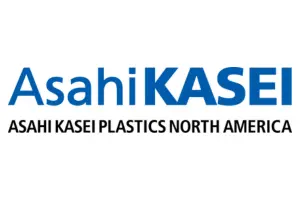
Asahi Kasei Plastics North America Pairs eMaint X5 and Power BI to Hit 95% On-Time PM Completion
The automotive plastics manufacturer moved seamlessly to eMaint X5 and now uses reports and dashboards to track performance across multiple sites.
Customer Since: 2012 | Industry: Automotive
BACKGROUND
Headquartered in Fowlerville, Michigan, Asahi Kasei Plastics North America is a plastics compounder that manufactures plastic pellets for automotive manufacturing, healthcare, and other industries. Most cars on the road feature their plastic.
Today, Asahi Kasei Plastics North America has 45 people using eMaint X5, including maintenance technicians and lab workers. The company began using eMaint more than 10 years ago, when they wanted a more streamlined alternative to pencil and paper to manage preventive maintenance on their equipment. Reliability Engineer Holly Trpik led the migration to X5 in 2022.
CHALLENGES
The move to eMaint X5 was prompted by a few factors. Asahi Kasei Plastics North America has multiple facilities: One in Fowlerville, Michigan, and one in Athens, Alabama. Between the two sites, the team manages approximately 2,000 assets, including extruders, feeders, hoppers, and plant support equipment. The plant support equipment consists of critical assets that service multiple lines, which means that when it goes down, multiple lines can’t run.
Both of these facilities share many of the same parts, processes, and equipment, so they needed a CMMS solution that would allow them to seamlessly manage multiple plants on one system. “We really liked the fact that we could have multiple plants on one system,” said Trpik, “Instead of having to copy and paste into both sites, I can just make one preventive maintenance task and then assign it to the assets from there.”
Another challenge the team at Asahi Kasei faces is customer audits. Their customers rely on Asahi Kasei for the reliable delivery of plastic pellets. Those customers need to know that equipment is being properly maintained, and that critical spare parts are kept on hand in case of a failure.
“Our technicians like to give me new ideas for things that will help make their lives easier,” Trpik says. “They’re excited about the fact that X5 has greater capabilities and customizations.”
IMPLEMENTATION
eMaint X5 offers visibility and transparency to internal and external stakeholders through centralized dashboards and reports to help the Asahi Kasei team stay on track and on time with their preventive maintenance tasks—a major focus for the team.
“Since we started tracking our preventive maintenance completion last year, we have an over 95% on-time completion rate,” Trpik said. The reporting dashboards also make it easy to respond to customer audits, demonstrating to customers that the equipment is well-maintained and that the appropriate spare parts are in inventory.
Asahi Kasei Plastics North America primarily uses eMaint to track work orders and completion reports. However, they also use eMaint for quarterly cycle counts of their inventory to ensure that their physical on-hand inventory matches. While the maintenance department is the biggest user of eMaint, lab technicians also use it to maintain calibration tasks at the right frequency.
RESULTS
“eMaint’s reporting has really helped us become more effective as a maintenance team,” Trpik said. “We have dashboards created so the technicians can see where we’re at as a team, and we also look at it on an individual basis.” This ability to easily track and trend metrics has become one of the most powerful benefits for Asahi Kasei Plastics North America.
They have also integrated eMaint with their existing software systems and tools, in order to streamline their business processes and ensure seamless data sharing. For example, Asahi Kasei Plastics North America uses Power BI, a data visualization tool from Microsoft, with eMaint.
With Power BI and eMaint, the team can review work order completion rates, comparing metrics from both the team as a whole and at the individual technician level. They can even see how their sites are performing side-by-side. They also leverage the Power BI configuration to look at preventive maintenance completion as a whole, as well as review late metrics and downtime.
OUTLOOK
“One of the features the techs really enjoy is that when an operator puts in a work request, the entire maintenance tech team gets an email with that work request attached, as well as some details. If they’re on the go in the plant, they don’t have to go back to a computer to see if any new work requests have come in.“
– Holly Trpik, Reliability Engineer at Asahi Kasei Plastics North America