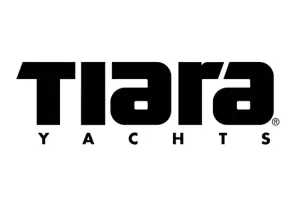
Tiara Yachts Maintenance Staff Saw Immediate Payback with eMaint CMMS Reporting and Dashboards
Customer Since: 2009 | Industry: Manufacturing
Tiara Yachts is a leading manufacturer of high quality yachts. The company implemented eMaint CMMS in 2009, in need of a way to name and catalog assets, and number parts. Tiara Yachts experienced diverse advantages using eMaint, including a reduction of training costs due to the ease of use, a “legitimized” maintenance staff, and an auto-generated year-end summary of maintenance activity for the first time in company history.
BACKGROUND
Tiara Yachts is a leading manufacturer of high quality yachts, based in Holland, Michigan. Tiara implemented eMaint CMMS to track labor activities of the maintenance department. They have created numerous reports and dashboards that enable them to spot trends and discover cost-saving opportunities.
THE CHALLENGE
At the time of their CMMS implementation, Tiara Yachts had three sites, 800,000 square feet of manufacturing area, over 400 employees, and hundreds of assets to maintain. They were in need of a scheme for naming and cataloging assets and numbering parts. The primary goal was to understand exactly what the maintenance department was responsible for, and then aggregate that information for the operations team and the owner of the company.
IMPLEMENTATION
Tiara implemented the eMaint CMMS system in 2009 and the transition went smoothly. They immediately began to catalog their assets in order to locate inventory more efficiently. Tiara also began building and scheduling preventive maintenance (PM) tasks for assets. After understanding the system and organizing their assets, Tiara began to charge labor costs directly to assets for the first time in the company’s history.
They ran reports on these findings in order to determine which assets required the most maintenance and which were the least costly to maintain. For example, Tiara was able to isolate and replace the specific components of their Chopper Rig that were consuming unnecessary resources.Currently, Tiara uses eMaint for tracking labor charges on scheduled PMs, work requests and repair work orders and are planning to utilize the inventory and purchasing (including barcoding and MX mobile) features of eMaint CMMS next.
RESULTS
eMaint helped Tiara satisfy their initial goal of cataloging assets in order to locate parts more expeditiously. Since implementing these tracking features, Tiara has been able to reduce expenses by identifying costly repairs and taking corrective action. In one instance, they identified a group of assets that comprised 6% of their inventory, but consumed 30% of the team’s resources. After running additional reports based on eMaint’s initial findings, the maintenance manager was able to isolate the cause (inadequate operator training), share this information with operations team and implement a revised training program. The need for this improvement would not have been evident prior to implementation of eMaint’s CMMS system.
One unexpected benefit of the system is the automated monthly reports, which helped to legitimize the maintenance team, giving them visibility to upper management. The maintenance manager is able to meet with the owner and show him exactly what his team has been working on in the past month. In fact, 95% of the maintenance staff’s available working time is registered on eMaint as recorded work time. After reviewing the length of time that the maintenance team has spent on each project, they adjust time allocation for improved efficiency. eMaint’s CMMS has enabled the maintenance manager to confidently recommend and gain approval on expenditures with solid data on anticipated cost-savings and payback.
BENEFITS
- Ease of use reduces training costs
- 95% of available work time is recorded and tracked
- “Legitimized” maintenance staff – provides decision support data
- Saved time and money by identifying need for more efficient components
- Generated a year-end summary of maintenance activity for the first time in company history
“For 30 years we didn’t measure anything. In the last 18 months we have built up that ability, and now we are able to trend just about anything we want. “
Dave L., Assistant Manager Facilities, Tiara Yachts