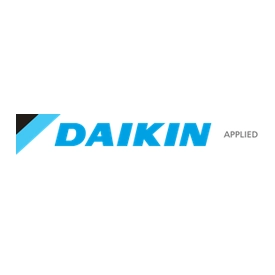
Daikin Applied Americas Centralizes Data and Inventory Management Across 8 Sites with eMaint X5 and Boosts PM Outcomes
Customer Since: 2022 | Industry: Commercial & Industrial HVAC Manufacturing
The company standardized maintenance across eight facilities with eMaint X5, streamlining preventive maintenance, boosting inventory accuracy, and improving operational efficiency.
Summary
Daikin Applied Americas (DAA) is a subsidiary of Daikin Industries, Ltd., the world’s leading air conditioning manufacturer. Based in Minneapolis, DAA specializes in advanced HVAC systems for commercial and industrial buildings and processes.
Before switching to eMaint X5, the company used a range of solutions for maintenance management across locations. However, the lack of standardization between plants led to increased downtime risk and higher maintenance costs.
After switching to eMaint, DAA now benefits from a centralized maintenance management system. Each of the eight facilities equipped with eMaint X5 has access to standardized data and tools, enabling consistent maintenance practices, better inventory management, and streamlined sharing of knowledge and resources.
- eMaint X5 centralized maintenance data from multiple sites into one CMMS
- Streamlined preventive maintenance for critical equipment
- Gave technicians the ability to work quicker and smarter with the Fluke Mobile app
- eMaint barcoding made spare parts inventory more accurate and accessible across facilities
- Dashboards provided a clear view of multi-site operations, allowing facilities to share best practices with each other
- eMaint customer service provided helpful and fast service during implementation
BACKGROUND
Daikin Applied Americas (DAA) is part of the world’s leading air conditioning manufacturer. The company’s equipment, solutions, and services, powered by innovative compression, refrigerant and heat pump technologies, deliver quality air to make work and living spaces more efficient, comfortable and sustainable.
DAA has multiple production sites in the United States that historically operated with their own maintenance and asset management protocols and systems. This decentralized approach presented significant challenges in maintaining consistency and efficiency across operations.
CHALLENGES
The fact that every DAA production facility used different protocols and systems meant that management across sites was difficult. With no set standards and the widespread use of software that wasn’t optimized for the factory floor, keeping things organized was a challenge. “We used many different products. We had MP2 and MP9 (maintenance software), for example, alongside some homegrown systems,” describes John Stepan, a master electronics technician at DAA in Faribault, Minnesota.
Nicholas Lasam, a scheduler/planner at DAA’s Staunton, Virginia site, highlighted further issues at his facility: “Our in-house system was built on Microsoft Access. Really, it was only useful for work orders and a little bit of downtime tracking. But it really lacked a calendar and schedules for PMs in the building.”
The array of disparate systems, each not providing all the necessary functionality, made it difficult to share information and resources. Managing inventory and spare parts was a notable problem too.
Furthermore, the absence of a centralized maintenance scheduling system made preventive maintenance more complex, heightening the potential risk of downtime. These challenges highlighted the urgent need for a more cohesive and streamlined way of working.
To fix these complex issues, DAA turned to eMaint X5.
IMPLEMENTATION
Implementing eMaint involved pulling together data from the array of DAA’s existing systems into a single, streamlined platform. This centralization aimed to achieve consistency across DAA sites while standardizing maintenance and inventory processes to boost organization-wide operational efficiency.
“Once we understood eMaint, we really took off with it,” says Lasam. “Now that we’re working with X5, we see the benefits. It’s simpler, better and quicker.”
eMaint specialists provided essential support during DAA’s transition to eMaint X5 — crucial for facilities upgrading from eMaint X4, as well as those completely new to the system.
“The eMaint team was helpful,” says Lasam. “Since we had so much information and so much data from X4, we knew that getting it into X5 was going to be a challenge. So, having a dedicated implementation specialist from eMaint was essential.”
RESULTS
Adopting eMaint X5 has helped DAA better connect assets, people and processes within and across its facilities, resulting in substantial improvements.
- Preventive maintenance is standardized: “It’s essential that all our critical equipment is getting the necessary PM so we can prevent disruptions and meet uptime targets,” says Lasam. To this end, eMaint X5 has streamlined preventive and reactive maintenance responses, improving DAA’s operational agility and keeping facilities running smoothly.
With eMaint, DAA sites can automatically track and manage the request and work order process for each asset, strategically prioritizing equipment based on its critical importance to operations. This has helped teams be more tactical about their preventive maintenance tasks. “We can create schedules based on where the team is most needed in the facility,” Lasam points out. “eMaint has helped us better align our day-to-day operations.”
At the Faribault facility, for example, the benefits of eMaint X5’s structured approach are clearly visible. Assets are tied to a rotating schedule, with each piece of equipment maintained according to the manufacturer’s specifications and tracked with the CMMS.
- Mobile app keeps technicians synced in real-time: By providing access to maintenance schedules, work orders and updates directly on tablets and phones via the app, technicians can “go through each procedure, make any readings that are necessary and track their time” says Lasam. This always-on capability improves coordination across the facility and makes every maintenance action timely and informed. DAA’s now-streamlined approach to maintenance makes it easier for technicians to coordinate work and complete it. “eMaint gives us the capability to quicken our response time,” says Stepan. “As soon as a work order is created, our technicians get a message on their phones that says, ‘Respond to this,’ and they can do so immediately.” Such real-time connectivity is essential for maintaining steady production and high asset uptime.
- Spare parts management streamlined thanks to eMaint barcodes: “There were times when we didn’t immediately know what parts we needed for certain equipment,” points out Stepan. Now, with eMaint, the ability to print barcode labels for any entity in the system streamlines the identification and management of necessary parts for each piece of equipment.
“As a technician, the inventory management features has been valuable,” says Stepan. “When we look up an asset, we know what we have in stock, how many we have in stock and where we can find that part in our warehouse.”
If a key part isn’t onsite, teams can simply check eMaint’s shared inventory to see if another DAA location has it. “In Minnesota, for instance, there are three sites within a 10-mile area,” says Stepan. “So, thanks to the CMMS, we’ll know that we can drive to another nearby plant to get a piece of equipment we need to continue production.”
Unified dashboards and analytics: Before eMaint X5, coordinating strategies across DAA’s sites was complicated due to inconsistent data and different operational standards. “We were all looking at different information,” explains Stepan. “It’s really hard to share data or strategies or insights when one site’s speaking ABC and another one’s saying XYZ”.
Now, with X5’s centralized reporting and standard benchmarks, everyone has access to the same data. Teams are working off the same page and speaking the same vocabulary, making it easier to take advantage of shared knowledge and duplicate best practices. “It helps us evaluate how we’re doing as a maintenance and facility crew, and aligns all sites so there’s visibility into how each facility is managing their uptime and asset downtime,” says Lasam.
As eMaint X5 continues to improve DAA’s operations, the system is set to expand. Half a dozen additional sites across North America are preparing to come online, aiming for greater synchronization and efficiency across the organization.
“There’s so much potential with eMaint. You can look at local asset information, work orders and work requests, but the ability to access and analyze data across the system provides another layer of value. I feel like we’ve just started to scratch the surface.”
– Nicholas Lasam – Maintenance Planner/ Scheduler at Daikin Applied in Staunton, Virginia
“The support from eMaint, in particular, has been excellent. If I have a technical question or need a report built, I always get an immediate response. And when I’m looking for something that’s non-standard and complex, a week later, all of a sudden, it’s done. Again, the support has been timely and helpful.”
– John Stepan, Master Electronics Technician at Daikin Applied in Faribault, Minnesota