Grand Prairie School District learns eMaint CMMS is a game-changer
Selecting and vetting a computerized maintenance management software (CMMS) system became a priority to help move from reactive to proactive asset management within a school system. Maintaining services for a school district the size of a major town is a massive logistical undertaking. That’s the challenge faced by Dianna L. Drew, Director of Logistics & Documents Services for Grand Prairie Independent School District (GPISD), and her team.
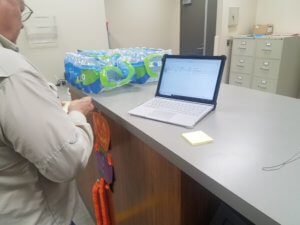
All images courtesy of GPISD
A 58-square-mile district near Dallas, Texas, GPISD employs 4,198 individuals, including 2,033 instructional staffers. GPISD serves more than 29,000 students on 38 campuses. The number of students is projected to grow substantially in the future.
With experience that includes work on the Boeing Corporation’s B-1Bomber and Saudi AWACS programs, Drew is well-acquainted with the intricacies of logistics. Three years ago, GPISD asked her to apply that expertise to district logistics issues.
As soon as Drew began her work, she identified multiple challenges. Drew explained, “For example, the [current] software couldn’t tell me ‘How much money have you spent repairing this unit?’ Assets weren’t controlled, and ticket systems were being run by failure solutions rather than preventive maintenance — a fundamental problem to solve.”
Doing the homework and passing GPISD’s mandatory tests
Drew and the GPISD Team reviewed scores of SaaS software packages to automate routine logistics tasks. “We took a lengthy approach to implementation and did a lot of homework,” stressed Drew. “After a solid year of research, we decided the Enterprise subscription level of eMaint™ computerized maintenance management software (CMMS) was the way to go.”
In addition to Drew’s own vetting, management buy-in from every department — including electrical, plumbing and HVAC — was mandatory. Team members, including senior staffers like the assistant superintendent, were asked to “beat up” and conduct “what ifs” to test the system. After this robust road testing, the team bought in.
Planning and training for smooth implementation
Changing the way an organization works can be an ordeal, but adding this CMMS was an exception. “I’ve implemented dozens and dozens of software packages over the years in different logistics roles,” said Drew. “By far, this has been the smoothest transition and easiest system to work with.”
One of the critical implementation success factors was preparation. “We made sure everyone was trained well before launch,” Drew explained. “For our techs who use tablets almost exclusively, we started by providing a guide with screenshots. Before they came to class, we gave them a work order, so they could ‘play’ with the system for three weeks. We then had a 30-minute live session for multiple groups of techs. For managers, we provided WebEx sessions with eMaint. Just in case, we also had an expert from eMaint onsite the week we went live, but the launch couldn’t have gone better.”
Easing adoption with single sign-on, uncomplicated web forms, and system adaptability
Single sign-on has made work requests and ticketing less time-consuming. “We don’t have to create separate accounts because everything and everyone works with a single sign-on,” said Drew. “Users state what their problem is (an electrical, plumbing or moving request, for example) and the room number. That’s about all they have to do.”
The simplicity of the Enterprise eMaint interface supported adoption. “If campus secretaries had questions, a 30-second video clip and quick instruction sheet are all that was needed,” according to Drew. “In fact, I received emails from staffers who said ‘This is so easy!’”
A dedicated eMaint logistics coordinator was hired to take care of in-the-moment issues, but as Drew noted, “We make 60% of the changes ourselves. If we decide that there’s something we need to add or change, we can do that on the fly. It takes 30 seconds to add a field. It just works, and everything is seamless.”
When assistance is needed, Drew stated that there has never been more than a day to get set-up. According to Drew, “eMaint support is excellent: we can chat, email or make a phone call, and the support team is very responsive.”
Improving inventory control
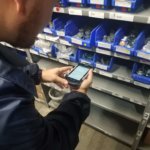
A logistics clerk uses a handhelp device to issue inventory
The most pressing task faced was taking control of inventory. “Information in our old system was so poor we couldn’t import the data into eMaint. We were dealing with a start-from-scratch situation,” said Drew. “We brought in a team that worked with us (through eMaint) to compile a complete inventory. With their help, it took only eight-to-10 business days, and I know it would have taken us eight-to-10 months to do without eMaint assistance.”
The previous system showed 10,000 inventory line items with multiple SKUs for the same part. After eMaint was in place, Drew could see that there were only 2,987 items in inventory. Drew reported, “I can also tell you that of those, 1,200 are electrical, and 456 are HVAC. Details like this are now accessible in real time.”
Making the move from location-based management to proactive asset management
The goal is to move from reactive to proactive asset management. “This level of inventory accuracy is a game changer,” Drew said.
According to Drew, maturing the system to shift from the building level “bird’s eye view” to work at the asset level will save even more time and money by extending equipment life with timely maintenance.
Saving time and 25% on subscription costs
Today, doing more with restricted budgets is vital for school districts of any size, anywhere in the U.S. “eMaint costs less than our previous CMMS. We’ve saved 25% in hard costs,” reported Drew. “The previous system lacked so many features and was inflexible — but subscription rates were higher.”
Even more than money, GPISD now saves time. In just six weeks, a workflow was in place with items automatically routed to the appropriate technician based on different campus assignments. Dispatch operators previously had to access every single ticket, manually determine what type of work was required, the location, and which technician to assign. Now as workflows are turned on, this is all completed automatically by the software.
Reducing work tickets and capturing labor costs
In a district like GPISD with more than 40 buildings, a high number of maintenance and repair tasks are requested that cover all types of systems: irrigation, plumbing, refrigeration, heating and ventilation, grounds issues, locks and keys, moving requests — all the way to graduation preparation. With the new system, the number is significantly reduced.
“Normally at this time (the end of the school year), we’d have had 700 or more work requests, but we have 584,” Drew related. “That’s because we’re now able to screen tickets and verify them before they become work orders. “
Understanding where and how work is accomplished and tracking it is a significant benefit of the new system. “Now every single ticket that’s come through and is closed has labor associated with it,” Drew explained. “We went from 0% labor costs to 100% because we now have reporting. Managers, who are required to check these tickets, know what’s completed and the backlog, too. The reports can be run automatically and emailed to specific people. In a short time, we’ve made huge strides in understanding how we need to work to achieve our goals.”
Paving the way for anticipated change and growth
Texas’ population, particularly in the Dallas area, continues to grow because of the lower cost of living, burgeoning job market, and excellent transportation. This is a trend that’s reflected in the increasing GPISD student population as well.
“We’re opening a new school at the end of July 2018,” said Drew, “We’ll have data from the building contractor, and using that data and eMaint, we’ll immediately flip to asset mode and build on that information for both current and future facilities.”