Equipment Maintenance Software
Manufacturing CMMS Software that Simplifies Work Management and Reduces Downtime
Easily track assets, repairs, and key performance indicators with eMaint CMMS.
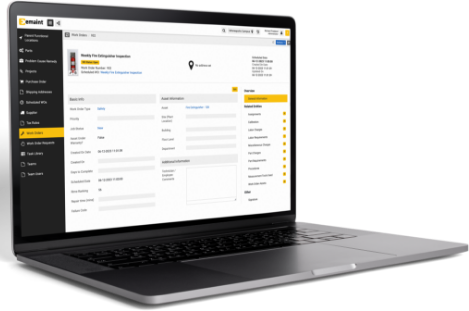
Meet eMaint, the award-winning CMMS equipment maintenance software that helps you maximize uptime and efficiency. eMaint simplifies tracking work orders, heavy equipment, construction and building materials, and KPIs. Plus, streamline work management with features like drag-and-drop scheduling, automated cost tracking, and seamless integration with other tools and systems.
eMaint streamlines ticketing and service requests,
heavy equipment and construction asset management, and boosting productivity.
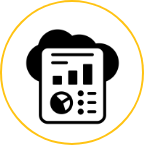
Reduce Unplanned Downtime
Predict machine failures before they occur with 24/7 condition monitoring and automatically triggered work orders.
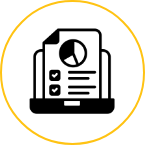
Say Goodbye to Paper PMs
Digitize work orders, floor plans, asset management, PM scheduling, and reporting — all in one place.
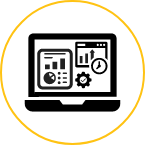
Easily Generate User-Friendly Reports
Gain visibility into KPIs like response times, work order completion, MTTR, MTTB, OEE, and more.
Our manufacturing preventive maintenance experts will tailor an equipment maintenance software package to your needs.
Top 5 Benefits of eMaint for Manufacturer Equipment Maintenance

Save Time on Daily Activities
Effortlessly manage work orders, asset hierarchy, and spare parts with drag-and-drop preventive maintenance calendars and interactive floor plans at your fingertips.

Maximize Uptime of Construction & Heavy Equipment Assets
Reduce costs, improve asset reliability, and maximize uptime. Monitor conditions like temperature and vibration in real time, and automatically trigger work orders at specified thresholds.

Easily Integrate with Existing Systems
Your maintenance and business processes work in harmony with easy API Integration, Low-Code Integration (ERP, CRM, and more), and SCADA, PLC, and BMS System Integration.

Work Across Sites, Languages, and the Globe
eMaint is invaluable for multi-site, multilingual, and international companies. Easily standardize processes, personalize user permissions, and tailor settings to each site, from language to currency to time zone.

Work On the Go with eMaint Mobile App
Manage work orders from anywhere, submit work requests by scanning QR codes on assets, and work offline in the field with confidence that all your work will be uploaded once a connection is available.
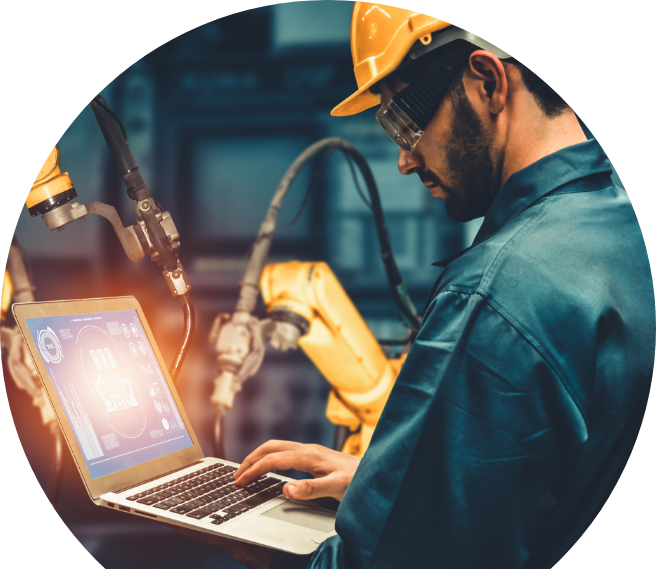
“One of the features the techs really enjoy is that when an operator puts in a work request, the entire maintenance tech team gets an email with that work request attached, as well as some details. If they’re on the go in the plant, they don’t have to go back to a computer to see if any new work requests have come in.”
– Holly Trpik, Reliability Engineer at Asahi Kasei Plastics North America
Our Most Loved Tools for Manufacturing & Heavy Equipment Challenges
eMaint equips you with a wealth of tools for problems unique to manufacturing. Our team will tailor the software to your specific needs, whether you want to simplify your ticketing and service requests, monitor and track assets and spare parts, or better capture and act on data-driven trends. eMaint offers global customer support and the in-depth educational resources that you need to accomplish any goal.
“I am a firm believer in eMaint and Fluke Reliability. From your software to your vibration sensors, you guys are in the business of protecting assets.”
– James Kalinski, Facility Engineer at Advanced Atomization